700 Tons of AZ 36 A572-GR50 For Los Angeles Parking
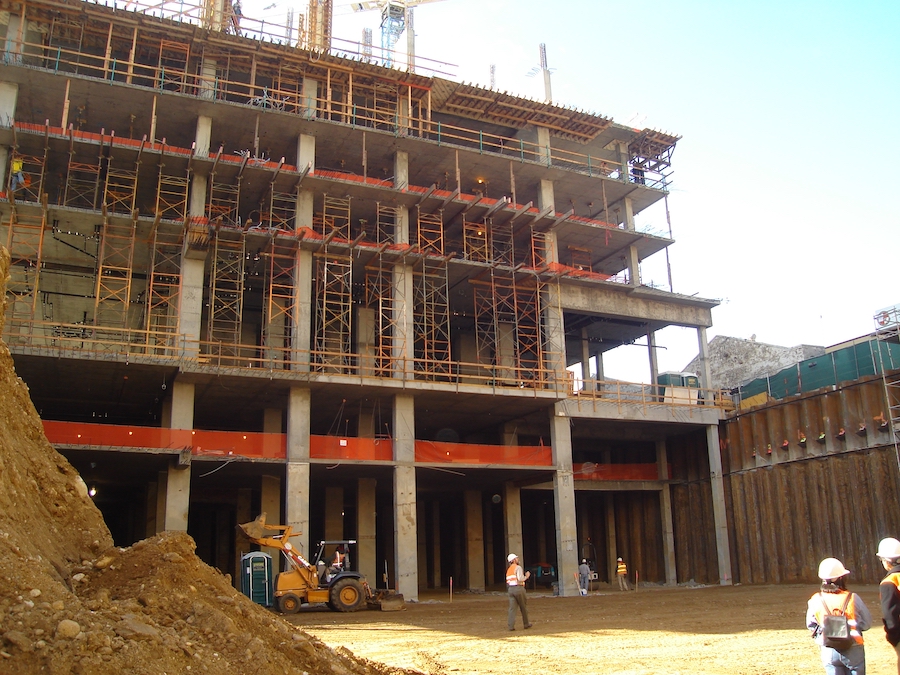
EVO – South: Mixed-use Residential/Below-grade Parking – Los Angeles, California
History
The City of Los Angeles began transforming the once-gritty downtown South Park neighborhood into the metropolis’ first-ever LEED-certified green community in 2003, and five years later the final phase — a 23-story tall condominium structure – was constructed.
The building overlooks the famous Staples Center, host to four professional sports teams, the Grammy Awards, major concerts, boxing title fights and political conventions. Incorporating a “green” theme, the loft style condos were designed to utilize sustainable materials and eco-conscious construction techniques.
Problem
Designs called for three levels of below-grade parking to be included in the EVO-South condominiums. Below-grade construction can be costly when utilizing conventional methods. The overall expenses incurred within the building process, including time and material, were turning out to be much higher than budgeted.
Driving steel sheet pile, traditionally done in sections with vibratory or impact hammers, can be a noisy process that often disrupts surrounding communities.
Solution
Nucor Skyline offered a versatile sheet pile solution that reduced costs and saved a significant amount of time over conventional construction methods.
As the third, and largest, of the three-block development, EVO-South houses 311 residential units and 627,000 square foot of space. In order to maximize the footprint, Howard Wright Construction utilized the innovative top-down construction method to build three levels of below-grade parking. The steel sheet piles acted as temporary shoring and the permanent wall. This allowed for the construction of the superstructure to begin before the excavation was completed. The sheet piles also carried the vertical loads of the garage and the lateral loads for the building.
Skyline provided engineering expertise throughout the duration of the project and advised the use of AZ 36 steel sheet pile. Nonstructural seal welding of the interlocks not only provided a water barrier, but also acted as a vapor barrier against potential methane fumes.
Due to negative implications of loud hammering or vibration on neighboring buildings in the urban environment, as well as the presence of very dense (50 blows/3”) sands and gravels, a silent crush piler system was used. The crush piler system was able to hydraulically jack and drill the sheet piles into the hard ground with minimal noise and vibration.
Months were removed from the construction schedule through a modified up-down excavation sequence which allowed building of the superstructure to commence well ahead of conventional schedules. A significant return on investment savings were realized with an early project completion date.
Project Partners
Developers
The South Group
Los Angeles, California
Williams & Dame Development
Gerding Edlen Development
Portland, Oregon
Contractors
Balfour Beatty
Dallas, Texas
Howard S. Wright Construction Co.
Scottsdale, Arizona
Architect
GBD Architects
Portland, Oregon
Engineer
KPFF Consultants
Portland, Oregon
Products
700 tons of AZ 36 A572-GR50