Pile Hammer Maintenance and Troubleshooting Guide
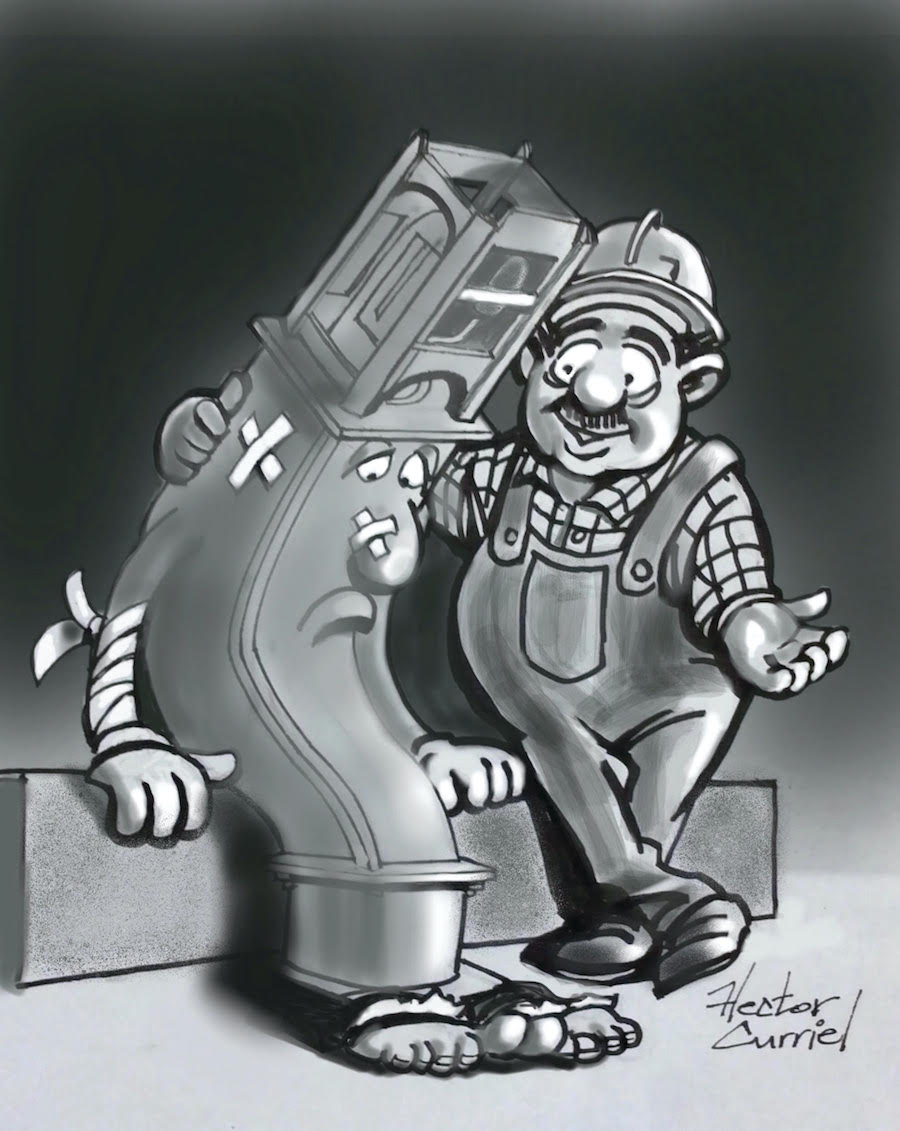
View the complete article here.
A focus on diesel hammers
Proper care and maintenance of your pile hammer is critical for safety. This guide covers common mistakes in hammer use and how to correct them. You will also learn to identify how a hammer was improperly used by examining the specific type of damage to it. This will help to inform train operators about the correct use, inspection, and troubleshooting of your pile hammer.
Common Pile Hammer Problems
Unintended Contact of the Piston and Catch Cap
What’s happening?
The pile hammer’s piston has a catch ring that mimics the behavior of a piston compression ring. If the piston is over-stroked, it expands and makes contact with an internal lip in the catch cap. This event ‘catches’ the piston and prevents it from exiting the hammer — an industry-standard safety feature for diesel pile hammers.
What to do
Hitting the catch cap is typically indicated by a sudden violent change in the rhythmic sound of the pile hammer’s hitting frequency. It is commonly accompanied by the hammer slightly lifting and slamming back down onto the pile. Anytime the catch cap is struck, immediately stop the pile hammer. Inspect the catch cap ring and ensure its stop edge hasn’t become rolled or chamfered. If it has, the ring will need to be remedied.
To prevent unintended contact of the piston and catch cap, we recommend performing a dry drop at the beginning of a shift. This will purge the cylinder of any diesel or oils that could have accumulated in the combustion chamber. See the pocket manual for dry drop instructions.
Remember…
Different pile hammer models will have different lengths of piston viewable out of the catch cap for the same running stroke or blow per minute rate.
Other possible sources of contact
- Not slowly increasing the fuel to achieve a desired blow count.
- Not closely monitoring blow count and decreasing fuel as necessary.
- Running the pile hammer too close to its maximum operating limit. (Refer to the hammer’s sales brochure for the limit.)
- Adjusting the oil pump to provide too much oil. This can result in a higher stroke initially after a period of downtime.
Identifying and repairing the piston hitting the catch cap end
FIGURE 1. This image shows the removable catch cap ring (found in newer models of our pile hammers) with evidence of it being hit. These rings can be flipped over if the opposite side has no damage. Otherwise, it must be replaced.
FIGURE 2. An older style catch cap (found in our older models of pile hammers), which has a stop edge feature machined into the catch cap. To repair this ring, separate the catch cap from the hammer. It can then be re-machined.
FIGURE 3. Hitting the catch cap can lead to crack formation on the catch cap groove on the piston. If this location is damaged, repair may not be possible.
FIGURE 4. A portion of the catch ring that has broken off because of a catch cap strike. This renders the catch ring ineffective in catching the piston. It leaves debris in the hammer that can damage the piston, its nose, and impact area. It can also severely score the cylinder’s bore .
Failing to Keep the Hammer Lubricated
The diesel pile hammer is basically a single piston engine. Just like a regular engine, you must properly lubricate the diesel pile hammer. The hammer has various moving parts that require lubrication, either periodically or constantly.
What’s Happening?
The oil pump is either not pumping oil into the hammer or is doing so too slowly. The piston must always appear a little wet, which can be seen through the trip slot located on the back of the hammer on the upper cylinder and/or as the piston rises out of the catch cap.
What to Do
The pump can be adjusted to deliver more oil. On a low stroke (~50 BPM), you can prime the pump by squeezing the prime ball that is feeding the oil pump. When this is done, it results in a temporary higher stroke in the hammer. This is normal. Refer to the hammer’s manual for further troubleshooting.
Remember…
Follow the pre-determined lubrication instructions in the pile hammer’s pocket manual. There may be an obstruction preventing grease from entering the hammer. Be sure to remove, then inspect the impact block greasing fittings and ports.
The table below is provided as an example and will not be regularly updated. Please refer to the hammer’s operation manual and/or hammer’s pocket manual.
Identifying and Repairing Damage Due to an Under-Lubricated Hammer
FIGURE 5. These pictures show a dry grease port. Even if there isn’t immediate damage, this is a clear indicator of insufficient hammer greasing.
FIGURE 6. A pile hammer that has little to no oil in it. This results in increased friction while driving. The driving energy is lowered, and the heat increases, causing stress within the hammer body. Pitting of the hammer bore and crack formation can result over time. This may require cylinder re-sleeving and/or weld repair of the external hammer body.
An impact block which has evidence of insufficient greasing. The outer body of the impact block shows evidence that it experienced a higher heat as a result (bluing of the metal’s surface). This can lead to higher stresses and can reduce the life of the impact block. All of the rings will also have to be replaced as they have lost their sealing ability due to collapsed piston rings.
A dry piston that was removed from a hammer. The piston can be viewed through the hammer’s trip slot, and the oil pump can be adjusted. If adjusting the oil pump is ineffective, consult the troubleshooting guide to repair the oil pump. This is similar to the end damage seen due to under-greasing the impact block. (Accelerated wear and premature ring wear.)
FIGURE 9. Trip rails that have not been greased regularly. This increases friction on the rails that accelerates wear on the trip gibs. It also requires more force to trip the piston, which gets transferred into the upper body of the pile hammer and may result in cracks.
FIGURE 10. Excessive wear of a trip gib due to a lack of grease. Extreme wear of the gibs can lead to the hammer not being able to trip out at the proper location.
FIGURE 11. The result of worn trip gibs. When the gibs are excessively worn, the trip assembly can operate further away from the hammer’s body. This results in the lift pawl not disengaging the piston and can damage the trip slot instead. Cracks can form in this location from the trip-hammer body contact. This is a non-repairable crack.
Insufficient Pre-Load Within the Cushion Stack
The hammer relies on the hammer cushion stack to isolate the pile-hammer interactions. This keeps the energy created from transferring to the hammer body and other hammer components.
What’s Happening?
During normal operation, as the cushions start to degrade due to wear and heat, the cushion stack will slowly lose its energy absorption ability and will start to lose its pre-load value. As the cushion stack starts to degrade, the cushioning lessens and hammer parts and hardware can start to crack and/or loosen.
What to Do
It is imperative to check the cushion stack pre-load. Try to insert a flathead screwdriver into the stack with minimal effort (50 psi). If the screwdriver cannot be inserted, the cushion stack is still good. If the screwdriver can be inserted, the cushion stack must be rebuilt. The Hammer Cushion Stack Build Procedure is found in the pile hammer’s operation manual. Refer to the specific model of hammer for process and layout of cushion rings, spacer, and required pre-load necessary to build the cushion stack properly.
Identifying and Repairing Damage Due to Insufficient Cushion Pre-Load
This cushion stack has not been assembled correctly per cushion stack build procedure. The bottom shows two new cushions, stacked up with four used cushions, followed by all the spacers in one location.
This will not distribute the loading through the stack properly. By not evenly distributing the aluminum spacers throughout the stack, the cushions will lose their elasticity more rapidly.
FIGURE 13. A stack that is well beyond rebuilding. The aluminum spacers, used for heat distribution, have started to break apart within the stack. At this point the cushions will have lost most of their energy absorption ability. All of the rings and spacers must be replaced.
FIGURE 14. Broken or loosening of bolts can occur when the cushion stack pre-load diminishes, which is a safety concern.
Hammer-Pile Misalignment
The hammer-pile is misaligned when the hammer and pile aren’t on the same angle. Severe or constant misalignment will damage the pile hammer. It will also run with a lower stroke.
What’s Happening?
Once the pile is in the ground, it is common that the pile will wander a little bit. It is likely that the hammer-to-pile alignment was not closely monitored.
What to Do
Site personnel must make the slight adjustments needed to maintain proper hammer-to-pile alignment while driving. A guide plate opening that is too small in relation to the pile size will also cause misalignment.
Evidence of Misalignment
- A loss of stroke.
- Damaged piles.
- Hammer body cracks.
- Loosening or broken bolts.
- Premature hammer gib wear.
Identifying and Repairing Damage Due to Hammer-to-Pile Misalignment
FIGURE 15. A guide plate with an uneven wear pattern. Considering where the marks are, it indicates that excess hammer forces are bypassing the cushion stack and are being applied directly to the hammer body.
FIGURE 16. The pile is riding the side of the drive housing, bypassing the hammer cushioning. This can load the hammer directly with driving energy, and the resulting misalignment can cause bolts to loosen or break. Components that were bolted to the hammer can fall out and result in injury or death.
Cracks can eventually form on the hammer body if the misalignment is not corrected.
Extreme misalignment over time can damage the direct-drive housing. In this case, the damage was irreparable, and the direct-drive housing needed to be replaced.
Misalignment of the hammer to the pile can cause an uneven loading condition on the moving parts between the hammer’s piston and the pile, specifically, between the direct drive striker plate, hammer impact block, and hammer cushion retainer ring. These pieces have been designed to take periodic minor misalignment. However, major or continuous misalignment will overload portions of the contact surface of the parts. This causes deformations. Although it is possible to repair minor misalignment-related wear, you will have to scrap parts with major deformations.
Exceeding 20 Blows Per Inch of Pile Penetration
What’s happening?
Exceeding 20 blows per inch pile penetration while driving over the rate of 40 BPM. Driving conditions may be requirements set through pile capacity testing and/or running the hammer below the rate of 38 BPM – high stroke – for over 20 minutes per pile . Although the hammer is capable of running in these states, depending on soil conditions, it may put too much stress within the hammer over time.
What to do
Exceeding 20 blows per inch of pile penetration to achieve the necessary pile capacity is an indicator that the hammer is undersized. An undersized hammer will need to be worked harder to achieve the final set of these piles. Also, the drive times will be much longer than using an adequately-sized hammer.
Running the hammer below the rate of 38 bpm over 20 minutes per pile is also an indicator that the hammer is likely too small to drive the piles. Site personnel may try to push a hammer to speed up drive time when soil conditions allow. This reduces equipment life. Damage to the pile hammer may result in downtime while the equipment is getting repaired.
When selecting a hammer size, pay close attention to the operating specifications found in the pile hammers’ sales brochures. You should contact the manufacturer for assistance.
Improper Installation or Tightening of Fuel Lines
Improper installation or tightening of fuel lines can cause premature failures or leaks within the fuel lines.
What’s Happening?
The main causes of improper fuel line installation are:
- Failing to use the two-wrench tightening method while connecting the lines to the injectors/fuel pump/manifolds or throttle blocks will make the line kink. This may lead to broken strands which can puncture the internal Teflon core. Or, it may add internal stress where the Teflon core and end fittings connect.
- There are sharp bends or excessive stiffness in the line lengths when installed onto the hammer. Each pile hammer has lines of a specified length to avoid excessive stress during assembly. Excessive twisting of the lines may cause the braid to become tight and unable to flex properly while the hammer is in operation.
- Insufficient clearance between hammer body and the fuel line. At no point, should the line make contact with the hammer body other than the end fitting connections.
- Excessive tightening/untightening of fittings. As with all threads, the more they are tightened and loosened, the more likely they are to fail.
Identifying and Repairing Damage Due to Improper Installation or Tightening of Fuel Lines
Fuel lines with visible fraying on the outer wire braid of the line are clearly damaged. However, what doesn’t show is possible fraying of the internal braids, which may puncture the inner Teflon core resulting in a fuel line leak. This is caused by the lines rubbing other components of the hammer or sharp bends or twisting in the fuel line, which cinch up the braids, making the line less flexible.
Broken fuel line stems can be the result of excessive tightening and untightening of the fittings. This can lead to fatigue cracking, which can propagate through the end connection. Excessive twisting of the fuel line can also result in strong forces being transferred to the end connection, which could cause failures.
Tripping the Hammer While Hammer is Running
Also known as “dogging the trip,” this is when the trip is lowered and engaged on the trip engagement lug. This results in the trip lifting pawl, pivoting within the bore of the cylinder while the hammer is running. This causes the piston (ram) to make contact with the trip lifting pawl with the driving force of the hammer.
What Is Happening?
Trips are operated by two methods:
Manual trip: A wire rope is connected to the trip and is directly controlled and positioned by the crane operator. This is done by controlling the rate of rotation of the winch to which the wire rope is connected. This method requires the crane operator to adjust the trip position while the hammer is running as the pile is being driven.
The common causes of dogging the trip in manual mode:
- Site personnel tie-off the trip leaver safety rope so the trip is always engaged. While driving the pile, the trip is lowered onto the engagement lug and engages the trip.
- Site personnel tie off the trip leaver safety rope, and there is an unexpected event, such as the hammer hitting the catch cap, causing the hammer body to jump. This takes up any slack in the trip leaver safety rope, and the engagement lug engages the trip.
- The crane operator lowers the trip body too quickly, causing a violent collision with the bottom part of the trip’s travel, which may result in the trip engaging.
Hydraulic trip: A hydraulic cylinder is connected to the hammer to move the trip up and down with the control of a hydraulic circuit within the crane or on a hydraulic powerpack. This tripping method doesn’t require adjustments while the pile is being driven. It is recommended that the hydraulic cylinders are fully extended if the hammer trip-out leaver isn’t able to swing-away from the hammer body or fully retracted if the hammer trip-out leaver is able to swing away from the hammer.
View the complete article here.
Why does pile hammer maintenance directly affect cost and project schedule?
Proper and regular maintenance and care of pile hammers is equally important as it drives the overall cost of equipment, project schedule, and also significant damage/life safety. Mismanagement increases the heat driving the hammer, less energy transferred to pile alignment, underutilization of hammer capacity, tool wearing.
What are common pile hammer problems?
1. Unintended contact of the piston and catch cap 2. Lack of Lubrication of the hammer 3. Insufficient Pre-load between pile cushion 4. Hammer-Pile Misalignment 5. Exceeding 20 blows per inch of pile penetration 6. Improper installation or tightening of fuel lines 7. Tripping of Hammer