Steel Sheet Piling Corrosion and Protection
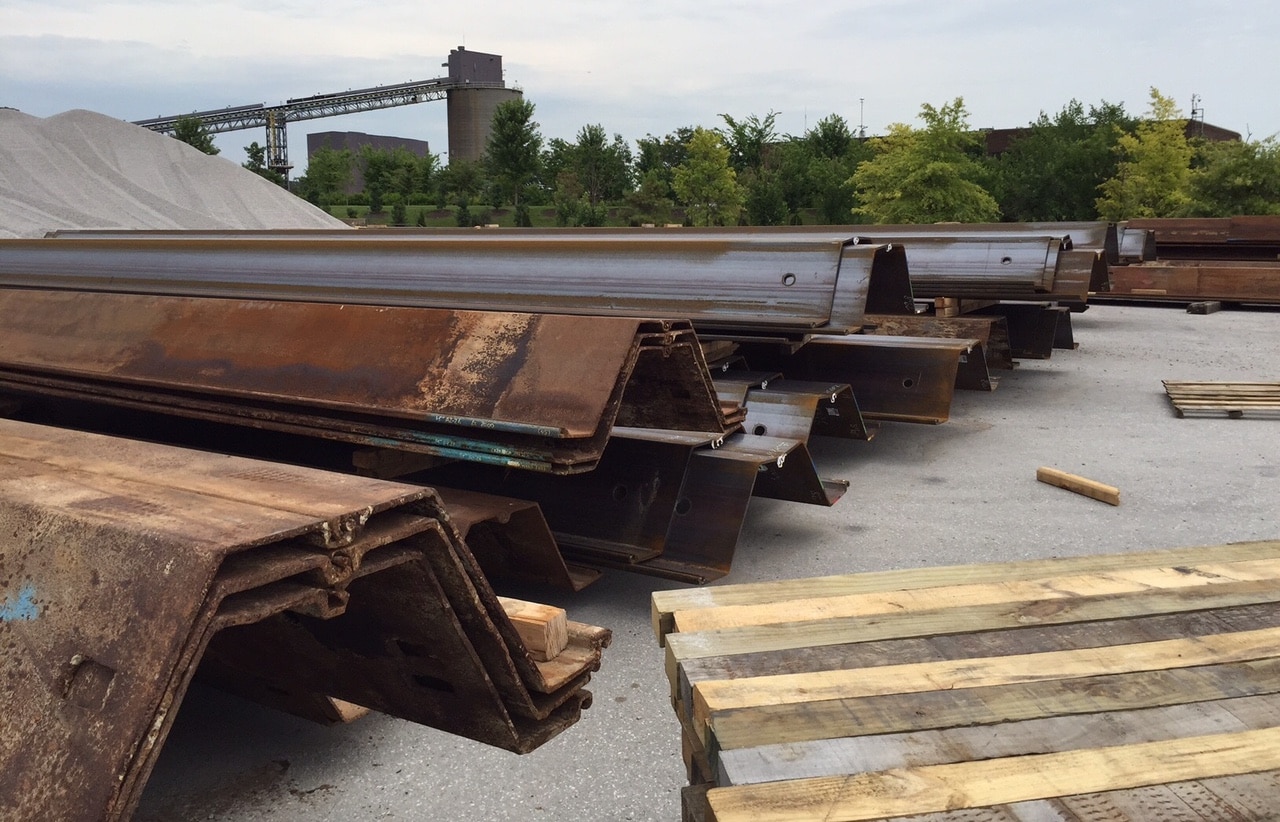
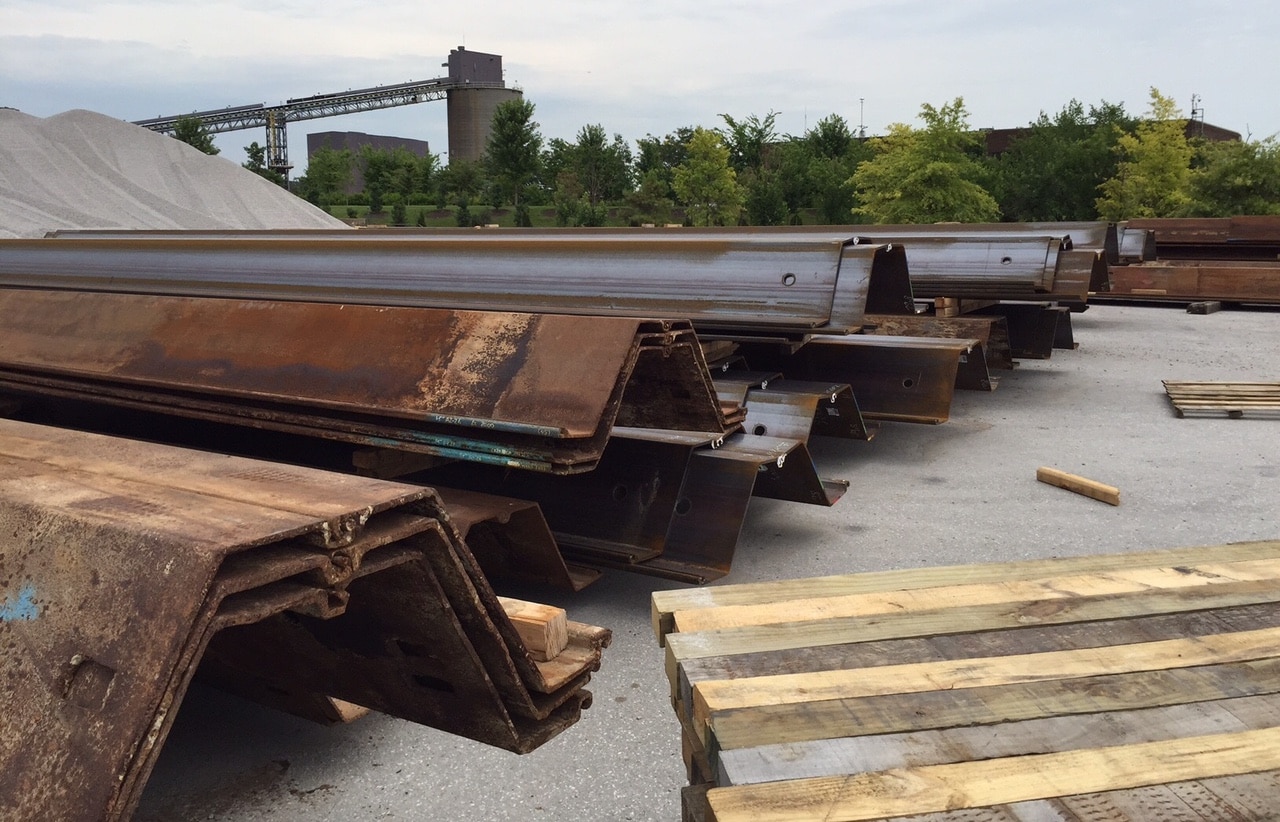
In marine construction environments, steel sheet pilings are exposed to a host of natural influences that can impact their useful service lives.
Corrosion represents one inevitable factor which engineers and marine contractors must consider when designing, installing, or working around these structural sections.
Because damage stemming from corroded steel can be significant, an understanding of corrosion factors, zones, and preventive measures is paramount to sustaining a piling’s long-term life.
Corrosion Factors
Moisture and oxygen represent the two main factors that cause corrosion, with the presence of moisture increasing the electrical conductivity of the environment in contact with the metal surface.
Chlorides: This is the principal reason for more aggressive attacks on steel and other metals in seawater, as chlorides escalate electrical conductivity and corrosion currents.
pH Value: This is the degree of the acidity of alkalinity in seawater, which typically ranges from 7.2 to 8.2.
Salinity: In the open sea, water has a salt content of about 3.5 percent. In unpolluted harbors and other seacoast areas, dilution with freshwater run-off occurs, yet the proportion of salts relative to each other remains the same.
Pollution: In harbors, pollution can include domestic sewage, complex industrial water, oil well brines, and spilled oil. When pollution destroys oxygen-dependent fouling organisms, corrosion rates can be unfavorably altered through permitting the survival of anaerobic bacteria. Contaminants that introduce sulphides or reduce pH at the sites of piles can elevate the corrosion rate of steel.
Wind: Gusts can alter wave action and carry salt-laden mist, with the residue of dried salt attracting moisture and continuing corrosion.
Rain: When retained in crevices, rain can stimulate corrosion by maintaining damp conditions.
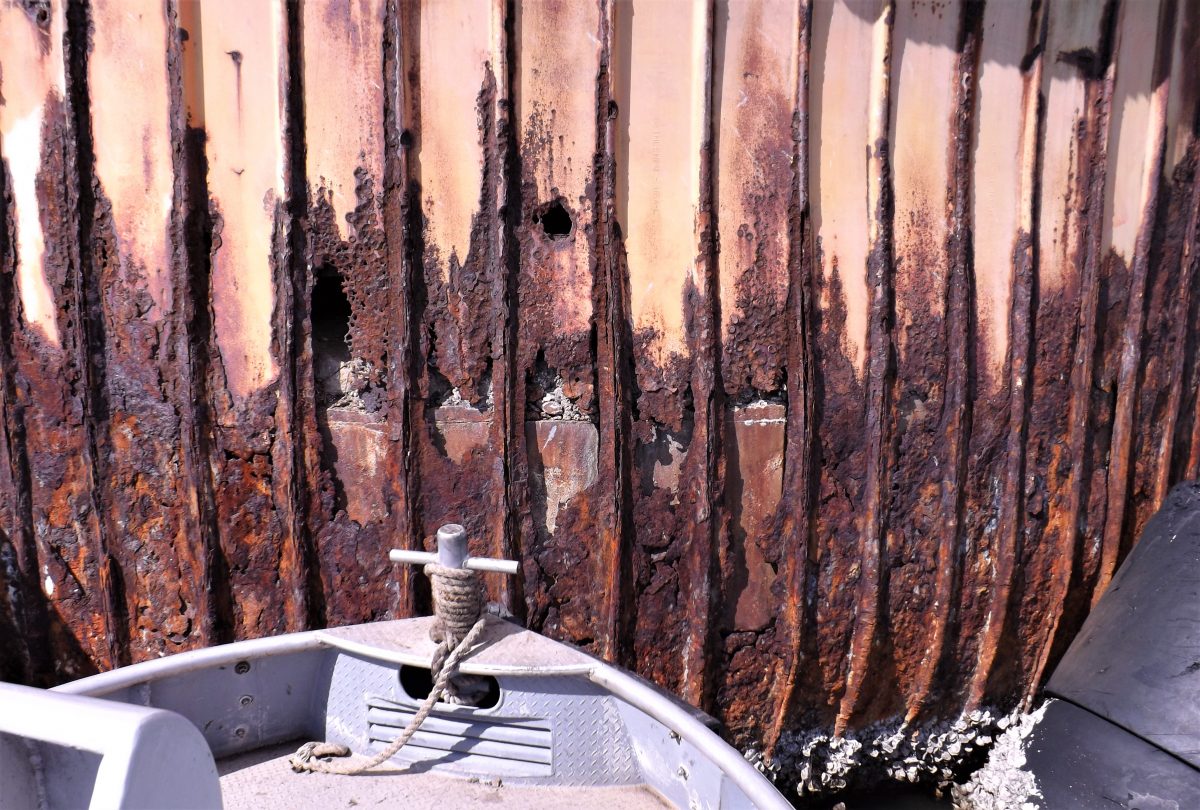
Corrosion Zones
Corrosion rates on steel piling surfaces vary considerably within five distinct zones.
Atmospheric Zone
The rate of corrosion in the atmospheric zone, where bare structural steel is exposed to an urban or rural environment, is dependent on the length of time moisture is in contact with a surface, the extent of contamination in the air, and the steel’s chemical composition.
The time at which a surface is wetted and the amount of chlorides in the atmosphere represent the most important factors in marine atmospheric corrosion.
The rate of loss in the atmospheric area within fresh water is very low. In saltwater, corrosion rates are influenced by distance from the ocean, rainfall, sunshine, and fog. In-ocean structures and those along the beach experience high rates of corrosion in this zone. Bulkheads built some distance from the beach boast more favorable rates.
Splash Zone
Considered the zone where the most serious corrosion activity occurs, the splash zone comprises the area of steel pilings at and immediately above the high tide line, which is subject to frequent wetting from splashing water.
Between this area and the immersed area, corrosion cells are produced by different oxygen concentrations. The metal underwater is anodic to the exposed area, with the corrosion rates intensifying because of the short electrical paths and tide changes.
Tidal Zone
An area of relatively low corrosion rates, the tidal zone is immersed on a part-time basis. The metal in this zone benefits from being cathodic to the metal which is slightly below low tide.
Continuously Submerged Zone
A shortage of dissolved oxygen at the water-metal interface equates to a low corrosion rate in both salt and freshwater areas that are fully immersed. A corrosion rate of 5 mils per year is used as a guide for carbon steel in seawater.
Buried Zone
Structures built of sheet piling obtain stability from being embedded into sound, natural soil, referred to as the buried zone. Some piling walls are driven into pre-existing soil. In these locales, corrosion is insignificant. Walls driven and then backfilled with dredged or trucked-in fill soil are subject to a higher rate of corrosion due to the oxygen content of these disturbed soils.
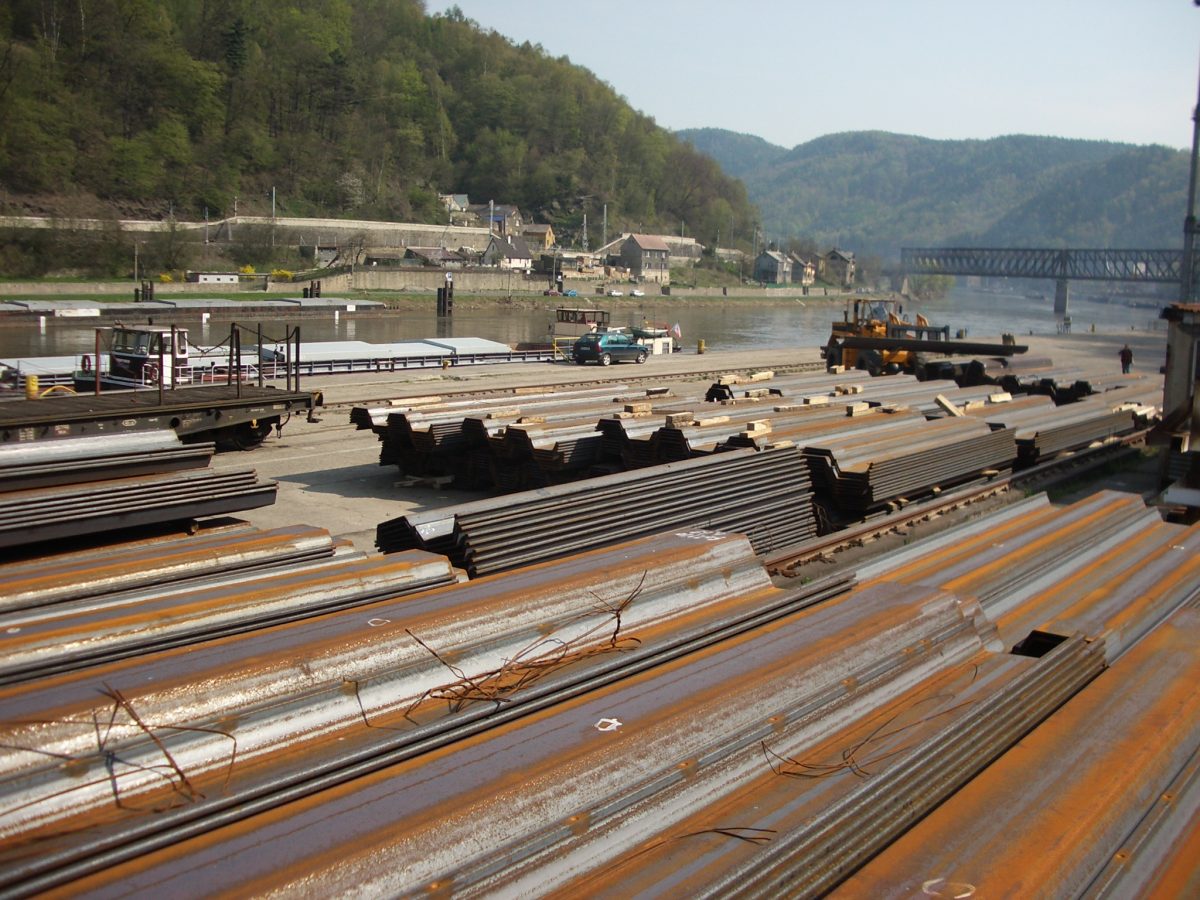
Types of Corrosion
Pitting Corrosion: This is a localized attack on a metal wherein the corrosion rate is noticeably higher in some exposed areas. The attack can result in broad, shallow craters or deep holes, and is frequently associated with pilings immersed in saltwater. This type of corrosion can also cause heavy pitting in tendons, which can lead to a reduction in cross-sectional areas and failure.
Uniform Corrosion: This is an equally distributed loss of metal that contributes to a reduction in the strength of the section, and potential failure by overstressing. Atmospheric and freshwater immersion-related corrosion is typically uniform. Uniform corrosion is commonly observed with tiebacks and tendons when stored onsite.
Galvanic Action: This entails the accelerated corrosion of a metal due to electrical contact with a more passive metal. In a seawater structure, coupling of dissimilar metals will cause galvanic corrosion to occur on the anodic member, with the cathodic member rendered inactive.
Stray Current Corrosion: Direct currents from improperly grounded welding generators, ship service systems, cathodic protection systems, and electric railway systems can cause stray current corrosion damage to ungrounded structures in a harbor area. One ampere of direct current passing from a structure to the seawater is said to remove approximately 20 pounds of steel in one year. Stray direct currents must be eliminated at their source.
Fatigue Corrosion: This is an enhanced failure of metal under the effects of corrosion and repeated or cyclical stress.
Bacteria and Fouling: A broken sewer or illegal discharge can leak anaerobic bacteria and cause accelerated corrosion at or near the mudline. Fouling occurs when barnacles, worms, and other biological organisms attach themselves to marine structures.
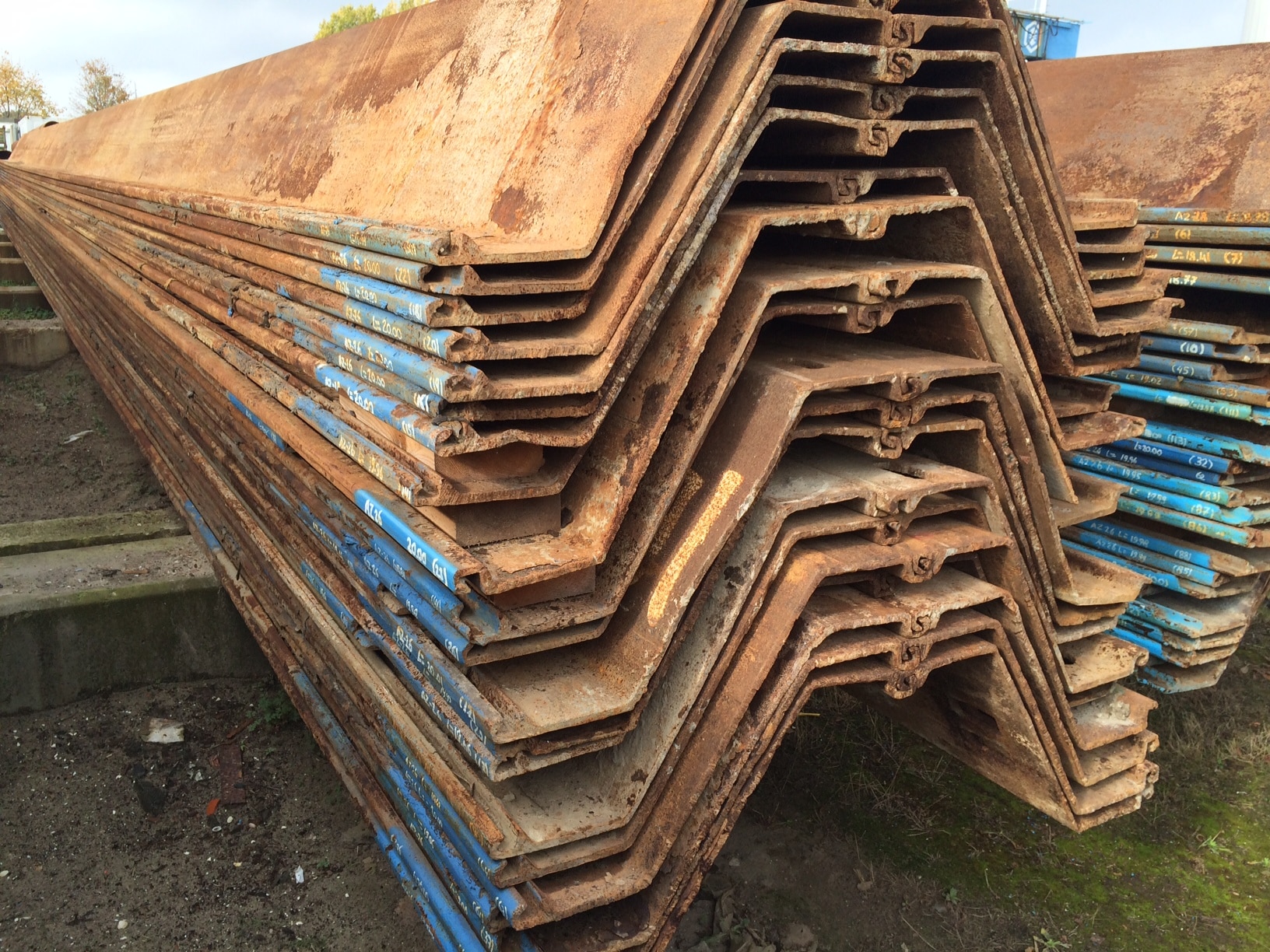
Protection
How aggressive a marine environment is will determine the extent of protections required, with all portions of a structure shielded in areas where the rate of corrosion is high.
Encasement of steel pilings in concrete is a common way to provide protection for both faces of sheet piling in the area extending from grade down to the average low water level, providing defense for the atmospheric, splash, and tidal zones. Encasement also provides a smooth face for the working zone of the bulkhead.
Protective coatings are routinely utilized and applied by brush, roller, or spray, with brushings of prime coats onto the steel achieving surface penetration. Protective coatings can be specified for one side, both sides, or selected parts of the pile, with the interior of the interlocks remaining uncoated.
When attempting to reduce the amount of current required for protection or to shield portions of the pile not covered in the splash and atmospheric areas, coatings can be used in conjunction with cathodic protection.
Non-Metallic Coatings
Most steel located in hostile environments is protected with non-metallic coating, with many organic and synthetic coatings and systems available. Non-metallic coatings are known for being cheaper on a first cost basis than metallic coatings, and more reliable than cathodic protection.
Metallic Coatings
Galvanizing: Accomplished by hot-dipping the item in a tank of molten zinc, galvanizing has not factored into the protection of most sheet piling in the U.S. due to costs; however, galvanized steel has performed fine in corrosion tests.
Flame Spraying: This is an old procedure where metal wire is fed into a hand gun, melted, and then blown by compressed air onto the surface to be protected. The molten particles alloy to the surface layers of the steel to form a tight bond.
Aluminum flame-sprayed coatings with film thicknesses of 3 mils and 6 mils, unsealed, provide complete protection in seawater and severe marine environments, with thin coat films offering better guarding than thick films.
Zinc flame-sprayed coatings with film thicknesses of 12 mils and higher, both unsealed and sealed, allow for complete protection in seawater.
Cathodic Protection
This type of guard involves the use of the galvanic series, which determines the nobility of metals when submerged, to prevent corrosion of the sheet pile wall. Utilized only in the fully immersed zone, cathodic protection can be difficult to maintain over an extended time. When implementing this type of protection, all piles must be bonded together to insure electrical continuity.
Sacrificial Metal Protection Method
Considered uneconomical and less effective than coatings and cathodic methods, sacrificial metal protection allows for extra material to be designed into the sheeting.
Special Steels
Adding certain alloys to carbon steel can enhance its performance in some marine environments; however, the application of weathering steels to sheet piling projects has not been practical because of its limited benefits in relation to cost.

Wales, Tie Rods, and Anchor Protection
Integral parts of a sheet pile’s bulkhead, wales and tie roads are subject to the same rate of corrosion as the sheet piling located on the embedded rear face of a wall.
Tie roads, like pipelines, are subject to pitting and uniform corrosion, and embedded in disturbed soil. Coatings and wrappings that provide for metal loss through oversizing are effective protective tools. When replacing deteriorated tie rods, install the new rods and turnbuckles one at a time. These fresh rods should be covered with a bituminous coating, a fabric tape, and then another layer of bituminous coating.
Wales are coated or galvanized when the embedded rear of the sheeting must be guarded, with holding hardware also galvanized or oversized to account for corrosion losses.
Anchors utilized for permanent applications must be protected in their free stressing length and at the anchor head.
Typically, a single degree of grease and sheath is required in the free stressing length, with Portland cement grout used to shield the tendon, bar, or strand in the bond zone. The tendon should have at least 0.5” of free length sheathing. Complete encapsulation of the anchor tendon can be achieved via a corrugated PVC or steel tube able to withstand deformation associated with transportation, installation, testing, stressing, and load transferring.
An anchor’s non-bonded length is commonly protected via a grease-filled sheath, heat shrink sleeve, or by secondary grouting after stressing.
The anchor head’s connection is the most critical area to protect from corrosion, as most anchor failures occur near the head.
A “trumpet” represents the typical solution. Comprised of steel or strong, durable plastic, the trumpet is used as a transition from the anchorage to the non-bonded length. One trumpet end is fastened and sealed to the bearing plate, with the other fitted with an O-ring. Anti-corrosion grease fills the space between the trumpet and tendon.
Bracing for the Inevitable
As with any steel, sheet piling will corrode during its life.
Accepting this and shifting focus on when, in what form, and at what rate this corrosion will occur is the way for engineers and contractors to secure a working knowledge of corrosion and prevention methods, enabling them to extend the useful life of sheet piling in various marine environments.
Why should I consider renting instead of owning steel sheet piling?
Renting can be more cost-effective and efficient, avoiding issues like unrecorded inventory, mismatched lengths, and difficulties in sorting and cleaning.
What are the common problems faced when owning steel sheet piling?
Common problems include unrecorded inventory reports, difficulties in identifying and managing pile types, mismatched lengths, and unforeseen challenges in using owned pile for specific project requirements.