Pile Driving Service | Pile Driving Service |
---|---|
Hulcher Services, Inc. | Foundations Masters, LLC |
More information | More information |
![]() |
![]() |
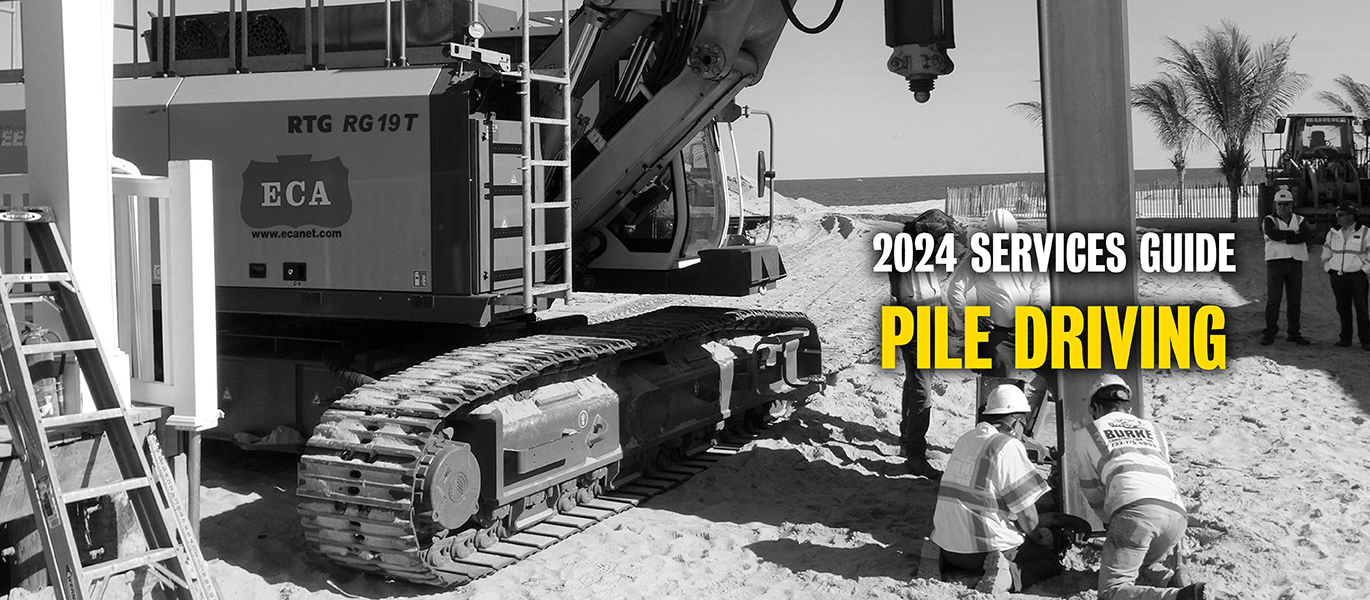
Pile Buck's Top Recommended Service Providers
Pile Driving Service | Pile Driving Service | Pile Driving Service |
---|---|---|
Hulcher Services, Inc. | Foundations Masters, LLC | Company 3 |
More information | More information | More information |
![]() |
![]() |
This guide is intended to serve as a resource for construction professionals who are involved in the critical task of pile driving. It offers a detailed look at the different types of equipment and methods available, provides practical advice on selecting the right tools based on specific project needs, and underscores the importance of adhering to rigorous safety standards to ensure both effective results and worker safety.
Pile Driving Equipment
Selecting the right pile driving equipment is paramount for successful project completion.
Types of Pile Driving Equipment
Pile driving is a critical task in construction that requires robust equipment capable of driving piles deep into the soil to form part of the foundation for various structures. The primary types of pile drivers used in the industry include…
Diesel hammers are traditional and widely used due to their reliability and power. Diesel hammers operate by dropping a heavy piston onto a pile using diesel fuel combustion to create the energy needed for the piston’s fall.
Hydraulic impact hammers are more modern and provide benefits such as reduced noise and better control. Hydraulic impact hammers use hydraulic fluids to move the piston, allowing for more precise energy delivery compared to diesel hammers.
Particularly effective in sandy or loose soils, vibratory pile drivers use vibration to reduce the friction between the pile and the soil—allowing the pile to be driven or extracted with less force.
Choosing the Right Equipment
Selecting the appropriate pile driving equipment is crucial to the success of any construction project. Here are key factors to consider…
Different soils have different characteristics that can affect the efficiency of pile driving equipment. For example, clay demands different equipment types compared to sandy soils due to its cohesive nature.
In urban or residential areas, noise can be a significant concern. Hydraulic impact hammers may be preferred over diesel hammers in such scenarios due to their quieter operation.
The scale of the project and the depth to which piles need to be driven also dictate the type of equipment needed. Larger projects requiring deep pile driving might benefit from heavier equipment with more power, such as large diesel hammers or deep-driving hydraulic systems.
The physical constraints of the project site may affect the choice of equipment. Sites with limited access or tight working conditions are likely to require more compact or easily transportable equipment.
Budget constraints are always a consideration. The cost of acquiring, operating, and maintaining pile driving equipment varies widely. It’s important to balance the initial investment against the expected efficiency, speed, and potential downtime to determine the most cost-effective solution.
Different regions may have specific regulations governing construction equipment, especially concerning emissions and noise. Ensuring that the chosen equipment complies with all local, state, and federal regulations is essential to avoid legal issues and potential delays.
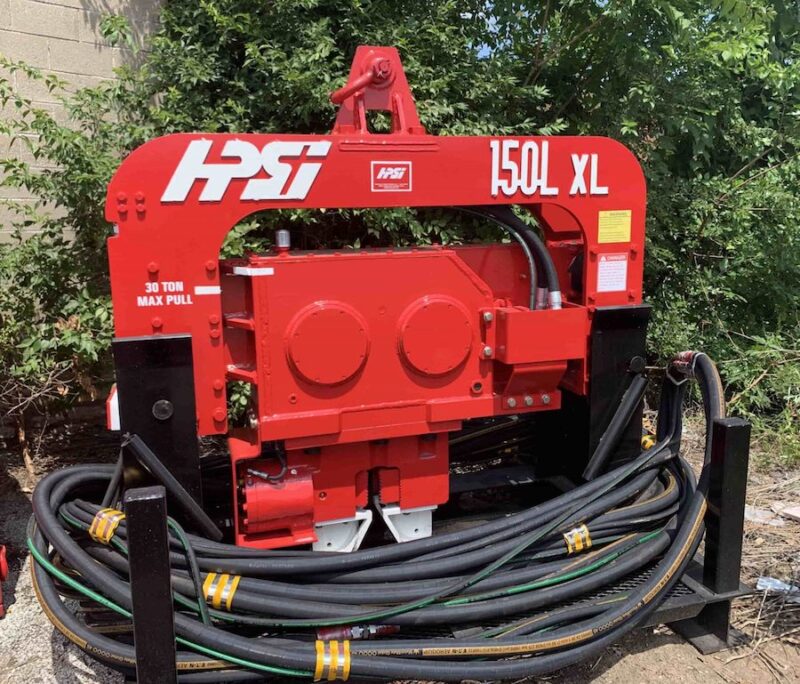
Pile Driving Techniques
Pile driving techniques are as varied as the projects that require them, each tailored to different soil conditions and project specifications.
Common Techniques
Pile driving techniques vary, each suitable for different types of soil and project requirements. Here are the most commonly used methods…
The impact driving method uses a heavy weight (hammer) dropped onto the pile to drive it into the ground. Effective for most soil types—it is particularly useful in dense, cohesive soils where the force can help overcome the soil’s resistance.
Vibratory hammers drive piles by rapidly vibrating them, reducing the soil’s resistance through fluidization. Best suited for granular soils like sand and gravel, the vibration allows particles to move apart—making it easier for the pile to penetrate.
Hydraulic or mechanical presses push piles into the ground without generating vibrations or noise. Ideal for sensitive environments where noise and vibrations must be minimized, such as urban areas or near historic structures.
Specialized Techniques
In addition to the common methods, there are specialized techniques adapted for specific conditions…
Jetting utilizes a high-pressure water jet at the pile tip to facilitate penetration in soft soil—particularly useful for underwater environments or very soft, silty soils.
Screw piles are turned or screwed into the ground, using a continuous helical surface on their shaft. This method causes minimal vibration and is used effectively in both load-bearing and tension applications, suitable for lightweight structures or temporary installations.
Removing soil to create a hole into which the pile is placed and often filled with concrete, drilled piles are used where traditional driving is impractical due to very hard soil layers or when minimal disturbance to the surrounding soil is necessary.
Safety Protocols in Pile Driving
In pile driving operations, managing risk and adhering to best safety practices are essential to ensure the well-being of all personnel and the overall success of construction projects.
Risk Management
Safety is paramount in pile driving operations due to the inherent risks associated with heavy equipment and high-impact activities. Here are the key safety risks and management strategies:
- Equipment failure:Regular maintenance and inspection of pile driving equipment are crucial to prevent failures that can lead to accidents.
- Falling objects:Implementing strict exclusion zones and using secure lifting practices can mitigate the risk of injuries from falling objects during pile driving.
- Noise and vibration:Prolonged exposure to high noise and vibration levels can cause health issues. Providing hearing protection and ensuring that all personnel are aware of safe operating distances are essential.
- Operator error:Comprehensive training for all operators and site personnel on the correct operation of equipment and safety protocols helps reduce the risk of accidents due to human error.
Best Practices
To ensure the safety of workers and the integrity of the project, the following best practices should be adhered to in pile driving operations:
- Safety training:All site personnel should undergo regular safety training and briefings specific to the equipment and techniques being used on the project.
- Personal protective equipment (PPE):The use of appropriate PPE (e.g., helmets, ear protection, visibility clothing) should be mandatory to protect against common hazards.
- Emergency procedures:Clear and well-practiced emergency procedures should be established to handle potential accidents or equipment malfunctions effectively.
- Safety monitoring:Continuous monitoring and auditing of safety practices on site ensure compliance and help identify areas for improvement.
- Communication: Regular communication among team members regarding safety checks, operational status, and any concerns is vital for maintaining a safe working environment.
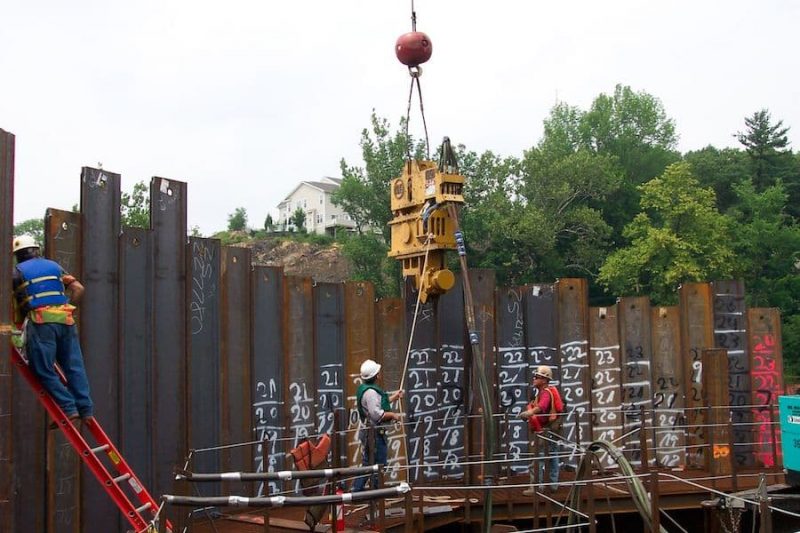
Troubleshooting and Maintenance
Proper maintenance and effective troubleshooting are critical for the efficient operation of pile driving equipment.
Common Issues
Pile driving operations can face several challenges that may affect productivity and safety. Here is an overview of frequent operational problems and their practical solutions:
- Equipment jams: Occurs when the pile driving equipment becomes stuck during operations. This can be caused by soil conditions or mechanical failures. Solution: Regularly clean and lubricate moving parts to prevent jams. Use appropriate driving techniques for the soil type to minimize resistance.
- Excessive vibration: Excessive vibration can lead to equipment wear-and-tear and can also be disruptive in sensitive areas. Solution: Ensure that all equipment components are properly aligned and tightened. Consider using vibration dampening techniques or equipment modifications.
- Hydraulic system failures: Hydraulic systems are crucial for the operation of modern pile drivers, and their failure can halt operations. Solution: Regularly check hydraulic lines and connections for leaks. Change hydraulic fluids at manufacturer-recommended intervals.
- Misalignment of piles: Incorrect alignment of piles can lead to structural failures. Solution: Use precise positioning technologies and ensure that the pile driving guide is correctly configured before starting operations.
Maintenance Tips
Maintaining pile driving equipment is essential to ensure its longevity and reliability. Here are some best practices:
- Regular inspections: Conduct thorough inspections of pile driving equipment before and after each use. Focus on critical components like hammers, hydraulics, and structural supports.
- Preventive maintenance: Adhere to a preventive maintenance schedule based on the manufacturer’s recommendations and real-time monitoring insights. Replace worn parts before they fail.
- Lubrication: Regularly lubricate all moving parts to reduce friction and prevent wear. Use the correct type of lubricant as specified by the equipment manufacturer.
- Operator training: Ensure that operators are well-trained in the proper use and maintenance of pile driving equipment. Knowledgeable operators can prevent many common issues through correct handling.
- Record keeping: Keep detailed records of all maintenance activities, repairs, and any issues encountered. This history can help diagnose recurring problems and improve maintenance planning.
Case Studies
In this section, we explore details of notable projects that have successfully utilized advanced pile driving techniques—along with the key lessons learned from each…
The San Francisco Bay Bridge Retrofit
- Project overview: Utilized vibratory pile driving to minimize disruption in an environmentally sensitive area, crucial in the densely populated and ecologically delicate San Francisco Bay area.
- Technique used: Vibratory pile drivers were chosen to install piles rapidly while minimizing noise and vibration.
- Lessons learned: The project highlighted the importance of environmental considerations in urban projects. The use of real-time monitoring systems proved invaluable, allowing for adjustments to be made on-the-fly—ensuring minimal environmental impact and maintaining structural integrity.
The Dubai Marina Towers
- Project overview: Employed hydraulic impact hammers to drive piles deep into the sandy and silty soils typical of the region, crucial for the structural foundation of high-rise buildings.
- Technique used: Hydraulic impact hammers were used for their precision and ability to reach necessary depths without disturbing the marine ecosystem.
- Lessons learned: This project underscored the need to balance efficiency and environmental protection. It demonstrated that advanced equipment could significantly reduce ecological disruption, setting a precedent for future construction in environmentally sensitive areas.
The Thames Tideway Tunnel
- Project overview: Jetting techniques combined with traditional driving methods were used to install piles in the soft clay of the Thames riverbed, enhancing installation speed and managing environmental impact.
- Technique used: A hybrid approach using jetting to soften the soil, followed by traditional driving for precise installation.
- Lessons learned: Adaptability and flexibility in technique selection based on real-time soil and environmental conditions can lead to better project outcomes. The project showcased how hybrid techniques could be tailored to meet specific environmental and soil conditions, promoting faster and more effective installations.
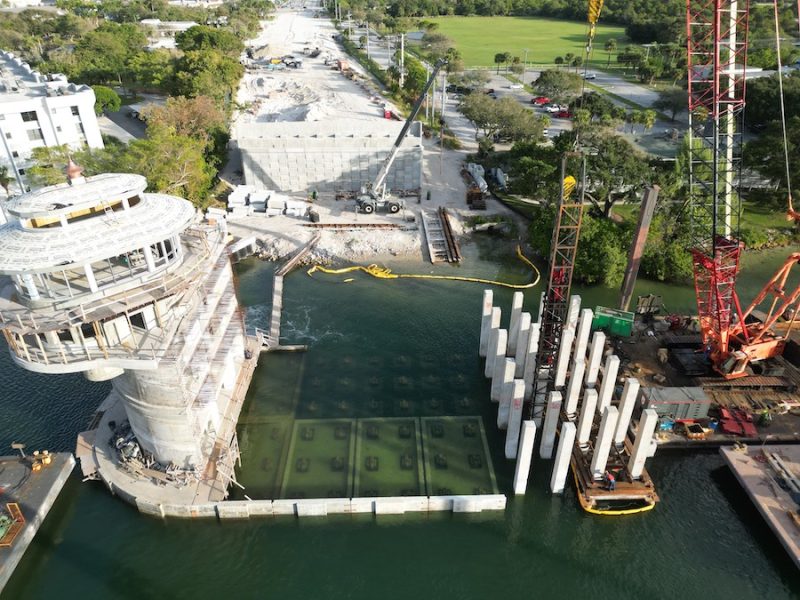
Service Providers and Contractors
Choosing the right pile driving contractor is critical to the success of any construction project. Here are essential tips to ensure you select a qualified and reliable service provider…
Look for contractors with a proven track record in the type of pile driving required for your project. Experience in similar soil conditions and project scales is particularly valuable.
Ensure the contractor holds all necessary certifications and licenses to operate in your region. This not only verifies their expertise but also their adherence to industry standards and safety regulations.
Assess the success of previous projects undertaken by the contractor. Request case studies or references to understand their capability and reliability.
Check if the contractor has access to the latest pile driving technologies and whether they are equipped to handle the specific demands of your project.
A contractor’s financial stability is crucial, especially for large or long-term projects. This can be a good indicator of their ability to manage and complete your project without disruptions.
Review the contractor’s safety record. A contractor with a strong emphasis on safety is less likely to encounter project delays due to workplace incidents.
Effective communication is essential. Choose a contractor who is responsive and makes an effort to understand and meet your project’s specific needs.
By following these guidelines, you can confidently select a pile driving contractor who will meet the demands of your project and uphold the highest standards of quality and safety.
PILE BUCK’S TOP RECOMMENDED PILE DRIVING SERVICE PROVIDERS
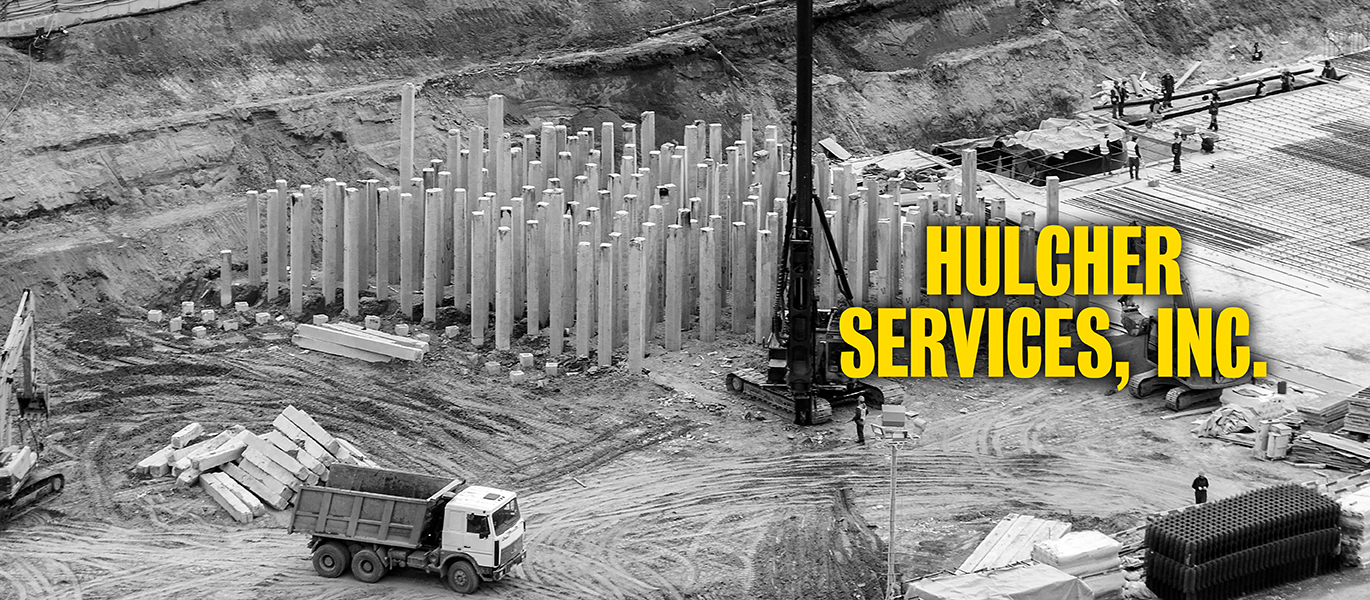
About
Hulcher Services, Inc. is a nationwide services contractor to the railroads, general industry and government with a commitment from our people for one purpose – to get the job done and done safely. Our headquarters is located in Denton, Texas and we have over 30 divisions strategically located across the United States and Mexico to provide our customers with the best service in the industry.
Our goal is to be the premier service provider for the freight railroads, passenger rail, general industry and government delivering safe, reliable and cost-effective solutions.
The Hulcher vibratory pile driver system provides outstanding driving performance for many foundation construction scenarios. The pile driver – also known as a vibratory hammer pile driver – is mounted to an excavator and operated by a single operator, with all hydraulic functions integrated to a simple joystick-mounted control.
Hulcher’s vibratory pile driver is an excavator-mounted attachment with an articulating side grip that speeds the pile driving process. The pile driver equipment uses the excavator’s hydraulics to quickly pick up, unload, place, drive and extract the piling. It is designed to overcome obstacles such as low overhead clearance and narrow passageways.
The vibratory hammer pile driver can be used for:
- Sheet Pile Driving
- Steel Sheet Piling
- Steel Pile Driving (i-beam)
- Railroad Track Driving
As a leading pile driving contractor, Hulcher can help with various types of projections nationwide including:
- Water Drainage Systems
- Soil Erosion Solutions
- Watering Erosion Solutions
- Drainage Services
- Bridge Stabilization Services
- Bridge Headwall Repair
- Grade Stabilization Services
When you need qualified railroad contractor professionals to perform pile driving services with the vibratory hammer for projects like water drainage systems, soil erosion solutions, weathering erosion solutions, drainage services, bridge stabilization services, bridge headwall repair or grade stabilization services, contact Hulcher at 833-316-0035 to speak with one of our customer service representatives.
Services
- Water Drainage Systems
- Soil Erosion Solutions
- Watering Erosion Solutions
- Drainage Services
- Bridge Stabilization Services
- Bridge Headwall Repair
- Grade Stabilization Services
Hulcher Services Inc.
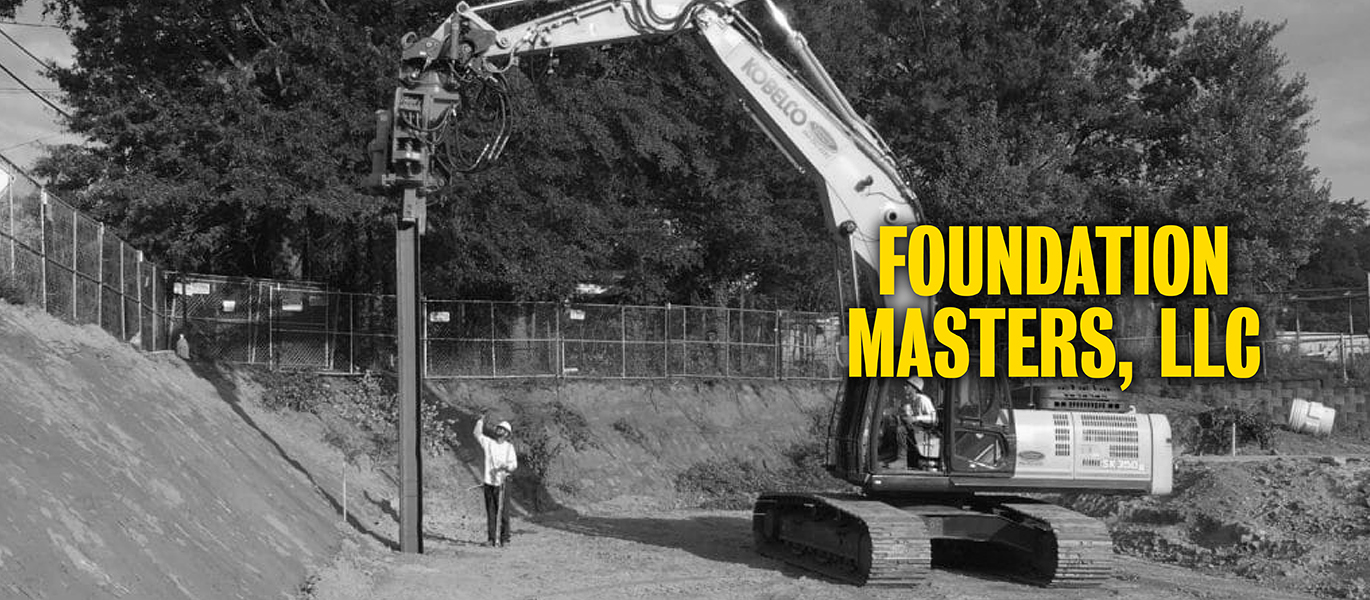
About
Foundation Masters, LLC Pile Driving Contractors and Engineers are the best design and build company in Florida. Foundation Masters, LLC Engineers and Construction staff have the experience and knowledge with all Pile construction and Pile Driving types and techniques in Florida. What this means is, we can design, install and test all types of Pilings through one company, no other contractors or engineers are needed. Our core group of people has been working together for years and I’m more than positive we have far more experience than competitors (Engineers & Contactors) in our area. Foundation Masters is unique in the large variety of Engineering and Construction services we provide through out the State of Florida. What else differentiates us from the competition is that we have the capability to take on large scale projects, but still provide personal service to the residential construction community.
If you are in need of Pile Driving Contractors or Pile Engineering, send over your drawings and soil borings and let Foundation Masters show you how we can save you money by value engineering at its finest. We can provide you with a revision to your foundation system as a specialty engineer. This is a very simple process that could save thousands of dollars and time. Our piling projects range from the most basics of residential foundations, to heavy commercial projects utilizing thousands of piles. We have vast experience engineering and driving all types of piles. We can manage any pile driving endeavor from inception to completion. Let Foundation Masters, LLC be your pile driving engineer and contractor in Florida.
Services
- Foundation Inspection
- Civil Engineer Florida
- Geotechnical Engineering Florida
- Structural Engineer
- Foundation Repair Florida
- Commercial Foundation Repair
- House Leveling Florida
- Seawall Contractors
- Bridge Construction Florida
- Crawl Space
- Pile Driving Contractors