Crane Repair Service | Crane Repair Service |
---|---|
North West Crane | Big Iron International |
More information | More information |
![]() |
![]() |
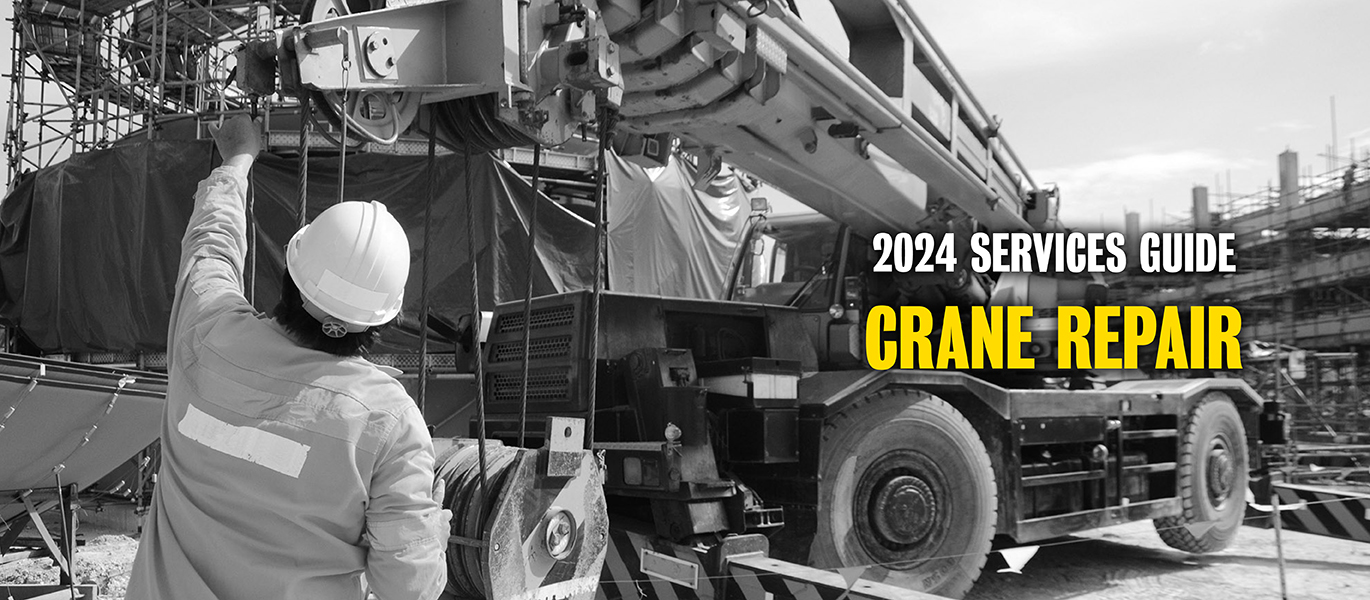
Pile Buck's Top Recommended Service Providers
Crane Repair Service | Crane Repair Service | Crane Repair Service |
---|---|---|
North West Crane | Big Iron International | Company 3 |
More information | More information | More information |
![]() |
![]() |
This guide is designed for contractors and other professionals who work in marine and foundation construction, providing a comprehensive overview of crane mechanics and maintenance. It explores the basic components of cranes, common mechanical issues and their symptoms, and offers detailed advice on preventive maintenance and troubleshooting.
Understanding Crane Mechanics
Understanding the fundamental mechanics of cranes is essential for maintaining their efficiency and ensuring safe operation in demanding environments like marine and foundation work.
Basic Components of Cranes
Understanding the mechanics of cranes is crucial for ensuring their efficient and safe operation. The basic components include…
The boom—the most visible part of the crane—is the long, telescopic or fixed arm that provides the leverage needed to lift loads. The type of boom (telescopic, lattice, or others) varies based on the crane model and its specific application.
Counterweights are used to balance the crane while lifting heavy loads, preventing the crane from tipping over. They are typically located at the back of the crane.
The hoist is the mechanism that actually lifts and lowers the load, often using wire ropes or chains. This component is critical and requires regular checks for wear-and-tear.
Outriggers are hydraulic or manual stabilizers that extend horizontally from the base of the crane to stabilize it during operations. They are crucial in marine and foundation work to ensure the crane remains stable on uneven surfaces or in challenging conditions.
The rotex gear is the component that allows the crane’s upper part to rotate on its base, providing the necessary movement to maneuver objects into place.
Positioned either at the top of the crane or at its base, depending on the design, the operator’s cabin is where the operator controls the crane’s movements.
Common Mechanical Issues and Their Symptoms
The most common mechanical issues associated with cranes include…
Symptoms of wear-and-tear in the hoist mechanism include unusual noises, slow hoisting speed, and slipping of the load. Regular inspection and replacement of worn-out ropes or chains are recommended.
Hydraulic system failures can be identified by leaks in hydraulic lines, unresponsive or erratic movements of the crane parts, and a noticeable decrease in lifting capacity. Keeping hydraulic fluids at the correct level and routinely replacing filters can prevent many hydraulic issues.
Electrical issues are typically manifested as irregular functioning of the crane, failure to start, or unexpected power shutdowns. Regular checks of the electrical wiring and connections, along with ensuring all controls are functioning correctly, are essential preventive measures.
Structural damage may include cracks or bends in the boom or other structural components, especially after heavy or repeated loads. These issues require immediate attention to prevent catastrophic failures.
Problems with outriggers can manifest as sinking into soft ground or failing to extend or retract properly, leading to instability during crane operations. Ensuring that outriggers are fully operational and used with appropriate ground support can mitigate these risks.
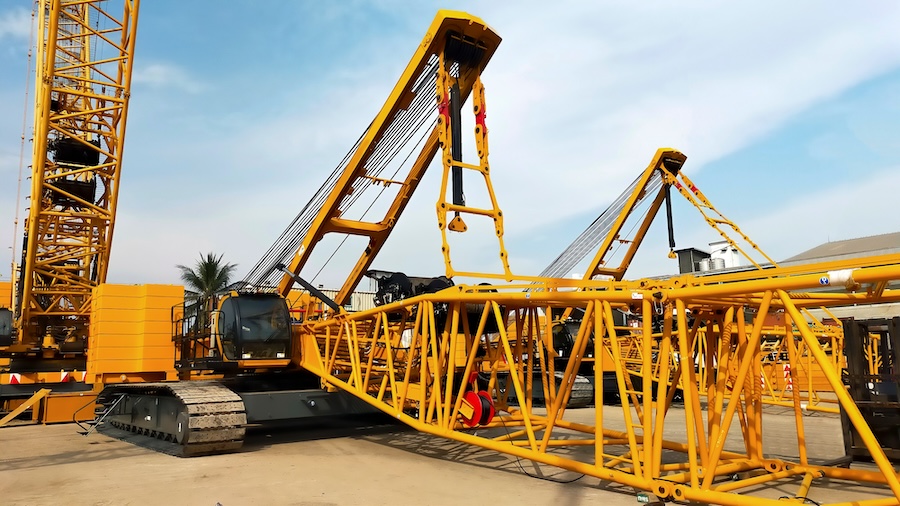
Preventive Maintenance
Preventive maintenance forms the backbone of operational safety and efficiency in crane operations, particularly in the demanding fields of marine and foundation work.
Detailed Preventive Maintenance Schedule
Preventive maintenance is crucial for ensuring the longevity, safety, and efficiency of cranes used in marine and foundation work. A preventive maintenance schedule should include:
- Daily inspections:Before any operation, a visual and functional check should be conducted to ensure there are no obvious defects or operational issues. This includes checking fluid levels (oil and hydraulic), inspecting for any leaks, and ensuring all controls are responsive.
- Weekly checks:
- Wire ropes and chains:Inspect for wear, kinking, or signs of fatigue. Lubricate as required to prevent corrosion and friction.
- Hooks and latches:Check for deformations or cracks that could compromise load security.
- Monthly examinations:
- Hoist mechanism:Test the hoist to ensure it operates smoothly. Check brakes and clutches for wear and proper adjustment.
- Outriggers and stabilizers:Ensure they are not bent or leaking and that they deploy smoothly.
- Quarterly reviews:
- Structural integrity:Inspect the boom and other load-bearing structures for signs of stress or cracks.
- Rotex gear:Check for smooth rotation and absence of grinding noises.
- Annual inspections:
- Conduct a thorough review by a certified professional to ensure all components meet industry standards and regulations.
- Review and update maintenance records and compliance documentation.
Importance of Routine Inspections and Compliance with Safety Standards
Routine inspections not only extend the life of the crane but also enhance the safety of operations. By catching issues early, operators can prevent minor problems from escalating into major failures that could lead to accidents or costly downtime. Compliance with established safety standards is non-negotiable, as it:
- Ensures the operational integrity of the crane.
- Protects the health and safety of operators and other site personnel.
- Mitigates legal and financial risks associated with workplace accidents.
Regular training sessions for maintenance teams and operators should also be implemented to keep them updated on the latest safety practices and preventive maintenance techniques.
Diagnostic Tips for Common Crane Problems
Effective troubleshooting and regular checks are essential for maintaining the operational integrity and safety of cranes.
How to Diagnose Hydraulic System Failures
To diagnose hydraulic system failures on cranes, consider this procedure:
- Check fluid levels and quality:Low or degraded hydraulic fluid can lead to poor system performance. Ensure the fluid is at the recommended level and has not become contaminated.
- Inspect for leaks:Leaks in hydraulic lines can cause a drop in pressure, leading to inadequate operation of the crane’s mechanisms. Visual inspections can help identify any leaks or cracks in the hydraulic hoses.
- Test pressure levels:Use a pressure gauge to check the hydraulic pressure against the manufacturer’s recommended settings. Abnormal readings can indicate issues such as clogged filters, faulty pumps, or worn seals.
- Listen for unusual noises:Sounds like whining or banging from the hydraulic unit can signal air in the system or mechanical failures within the pump.
Electrical Systems Troubleshooting
When it comes to troubleshooting electrical systems on cranes, consider the following procedure:
- Inspect wiring and connections:Loose or corroded connections can cause intermittent or faulty operation. Check all electrical connections for tightness and signs of corrosion.
- Test electrical components:Use a multimeter to test the continuity and voltage outputs of sensors, switches, and solenoids. Replace any components that do not meet the specifications.
- Check fuses and circuit breakers:A blown fuse or tripped breaker is a common cause of electrical system failures. Ensure they are in good condition and replace or reset as necessary.
- Review error codes:Many modern cranes are equipped with diagnostic systems that log error codes. Refer to the operator’s manual to interpret these codes for specific troubleshooting insights.
Structural Integrity Checks
Consider the following structural integrity checks for cranes:
- Visual inspection for cracks and corrosion:Regularly inspect the crane’s structural components—such as the boom and supports—for any signs of cracks, corrosion, or other damages.
- Load testing:Conduct periodic load tests to ensure the crane can handle the maximum rated load safely. This test can help in identifying any potential structural weaknesses.
- Check alignment and deformation:Misalignment or deformation in the crane’s structure can lead to uneven load distribution and increased wear. Use precise measurement tools to ensure all components are correctly aligned and undamaged.
- Consult with structural engineers:For any abnormalities found during inspections, consult with a structural engineer to determine the severity and necessary repairs.
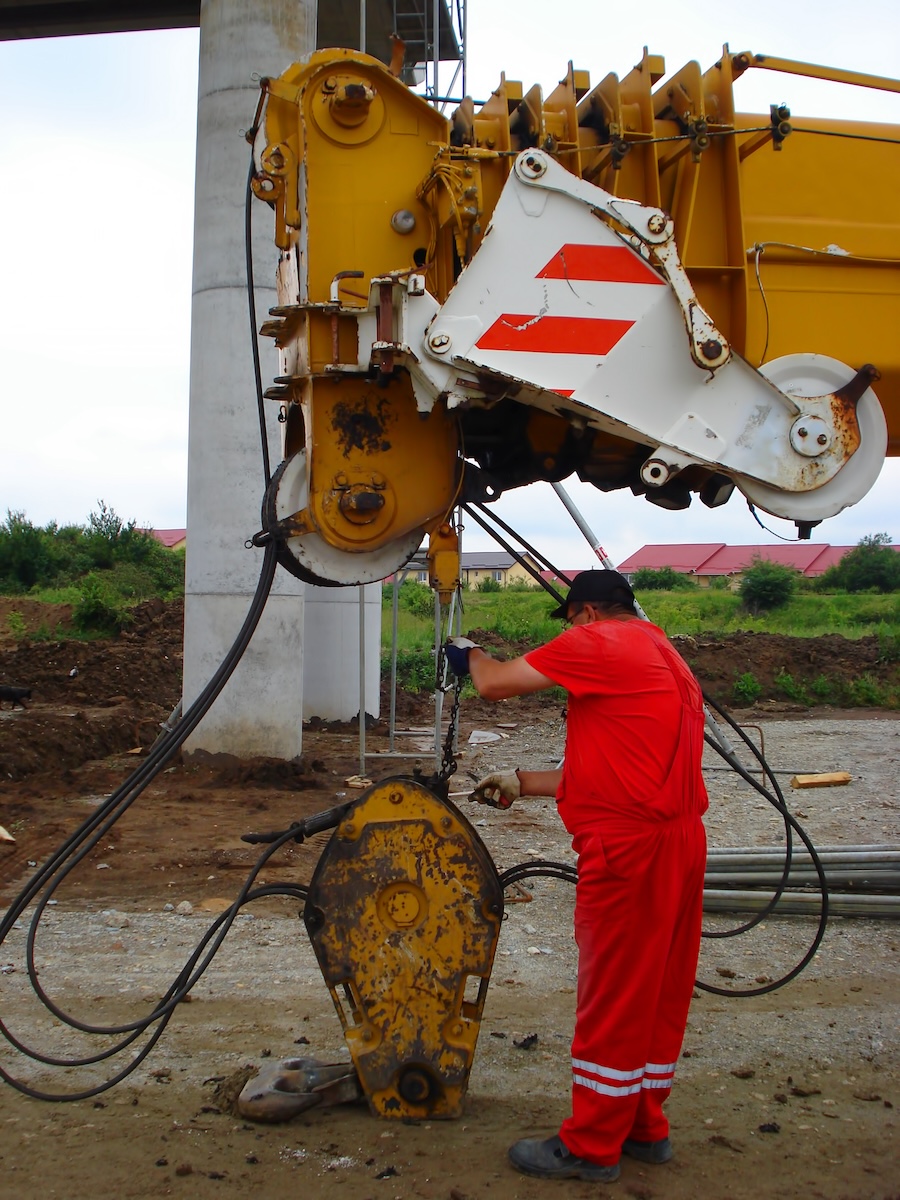
Choosing the Right Crane Repair Service
Selecting a competent crane repair service is crucial for ensuring the reliability and longevity of your equipment. Consider the following criteria for selecting a crane service provider…
Ensure the service provider holds all necessary certifications from recognized industry bodies. Certifications such as ISO 9001 for quality management or specific crane manufacturer approvals are indicators of a reputable provider.
Choose a service provider with extensive experience in repairing the type of cranes used in your operations. Familiarity with specific models ensures that the technicians are aware of common issues and are prepared with the right parts and tools.
Consider the provider’s availability for regular maintenance and emergency repairs. A service provider that offers 24/7 emergency services is preferable, especially for projects where downtime can result in significant financial losses.
Look for service providers with a good industry reputation and strong references. Testimonials from other marine and foundation projects can provide insights into their reliability and quality of service.
Evaluate the safety record of the service provider. Providers who adhere to strict safety standards and have a history of few accidents are preferable.
Case Studies
When it comes to crane operations, learning from real-world scenarios is invaluable. This section of the guide showcases case studies that illustrate effective crane repair and maintenance practices, along with the lessons learned and best practices recommended.
Case Study 1: Emergency Boom Repair on a Marine Site
Situation: A marine construction project faced a critical challenge when their main crane’s boom developed a significant crack during operations.
Action taken:
- Immediate cessation of crane operations to prevent accidents.
- On-site inspection by certified technicians who employed ultrasonic testing to assess the damage.
- The damaged section of the boom was swiftly replaced with prefabricated parts.
Outcome:
- The crane was back in operation within 48 hours, minimizing project downtime.
- A revised maintenance schedule was implemented, focusing on frequent stress-point inspections to prevent similar occurrences.
Lessons learned:
- Regular inspection of high-stress components can preempt major failures.
- Keeping a stock of critical spare parts on-site can drastically reduce recovery time from mechanical failures.
Case Study 2: Hydraulic System Overhaul in Foundation Crane Maintenance
Situation: A foundation project crane suffered from recurrent hydraulic failures, causing delays and safety concerns.
Action taken:
- A comprehensive audit of the hydraulic system was conducted to identify all fault points.
- All worn-out hydraulic hoses and seals were replaced, and the system was flushed and refilled with high-grade hydraulic fluid.
- The maintenance team received additional training on hydraulic system troubleshooting and maintenance.
Outcome:
- Hydraulic failures were reduced by over 90%.
- The crane’s operational efficiency improved, and the team was better prepared for routine maintenance.
Lessons learned:
- Preventive maintenance is more cost-effective than emergency repairs.
- Educating maintenance staff can lead to better upkeep and fewer operational disruptions.
Case Study 3: Retrofitting Electrical Systems for Enhanced Safety
Situation: An aging crane used in pile-driving exhibited frequent electrical outages that posed risks to operational safety.
Action taken:
- The entire electrical system was upgraded—including the installation of new wiring, sensors, and circuit breakers.
- Implementation of a real-time monitoring system to detect electrical faults before they cause failures.
Outcome:
- The incidence of electrical failures decreased significantly.
- The crane’s safety and reliability increased, boosting overall site productivity.
Lessons learned:
- Upgrading aging equipment and parts can significantly enhance safety and efficiency.
- Real-time monitoring systems serve as an early warning system to prevent potential failures.
These case studies highlight the critical importance of proactive maintenance and the benefits of learning from past experiences to improve crane safety and efficiency.
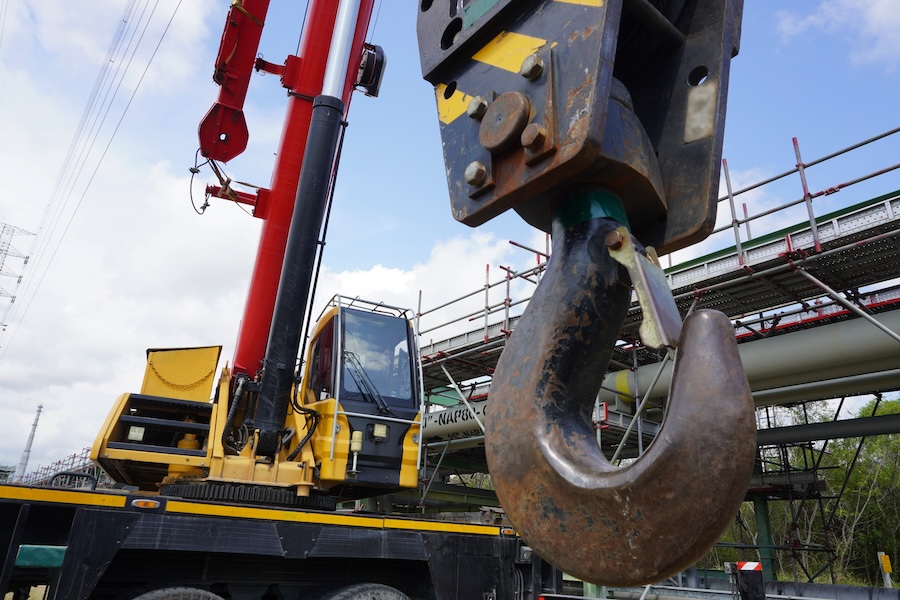
PILE BUCK’S TOP RECOMMENDED CRANE REPAIR SERVICE PROVIDERS
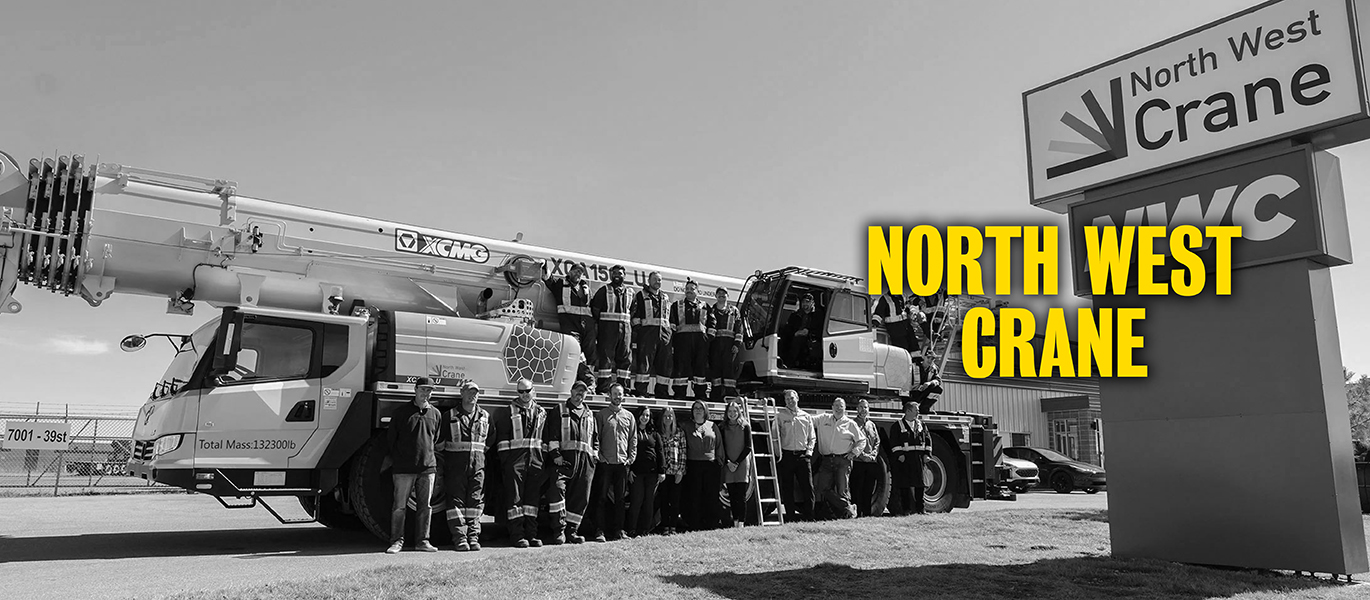
About
Founded in 1993, North West Crane Enterprises Ltd. has grown to become the preferred supplier of truck mounted cranes and specialty fabrication/rig-ups in Western Canada.
From our humble beginnings we have been focused on customer service, the core principle of our business. Never standing still, we innovate, customize and create solutions for our customers. With a foundation of dependable, quality service and honest value for your dollar, you will find North West Crane a friendly place to do business. We are mobile crane specialists, from reception to shipping and receiving. We are the exclusive dealer for Ferrari knuckleboom cranes and are the pre-eminent distributor for Weldco Hydralift, the preferred picker truck in the Western Canadian oilpatch. North West Crane offers you excellence in service, repairs, certification and replacement parts for all makes and models of truck mounted cranes.
In 2018, North West Crane signed an exclusive dealership agreement to represent XCMG mobile cranes in Western Canada. Xuchou Construction Machinery Group (XCMG) is the 3rd largest construction equipment manufacturer in the world and #1 on International Crane & Specialized Transport’s ranking of the world’s crane manufacturers. We are proud to represent this world renowned manufacturer and welcome your interest in truck mounted, rough terrain, all terrain and crawler cranes from 40 thru 4,000 ton capacity!
Services
- Crane Repair
- Custom Fabrication
- Sales
- Parts
- Other Services
North West Crane
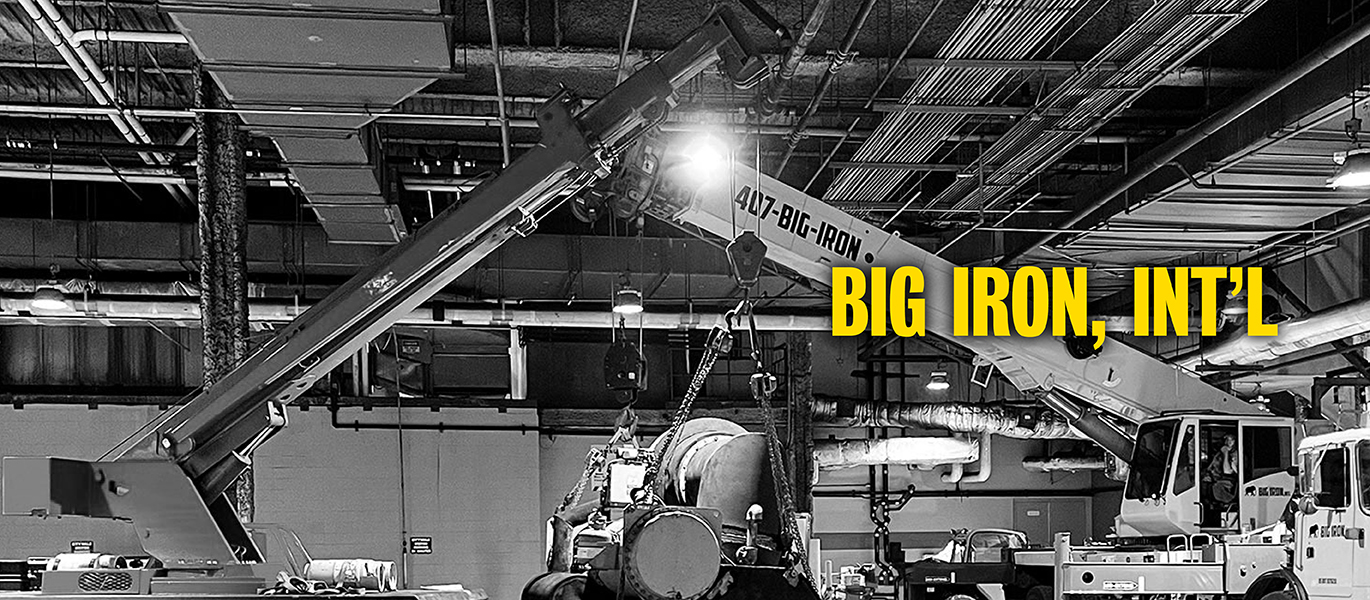
About
Big Iron International values our contractor, professional, government, and corporate clients. Your success is ours. We are committed to supporting you and being your go-to source for expert crane services.
We provide Commercial Crane & Lifting Services for
- Building Materials
- Construction Materials
- Machinery
- Columns
- Steel Beams
- Solar Panels
- Truck or Trailer Offloading
- Large Pipes
- Generators
- Utility Equipment
- Landscaping/Trees
- Large Components
- Safety Signage
- Shipping Containers
- HVAC Units
- Septic and Water Tanks
- Transformers
- Railroad Signs
- Water Fountains
- Boulders and Rocks
You can rely on Big Iron International for affordable and expert crane services for your commercial needs. If you don’t see what you are looking for above, please give us a call at 407-244-4766 and we will be happy to answer any questions and come out for a complimentary site visit to review your needs.
Services
- Crane Service
- Crane Rental
- Custom Crane Solutions