10 Tips for Enhancing Efficiency in Foundation Drilling Applications
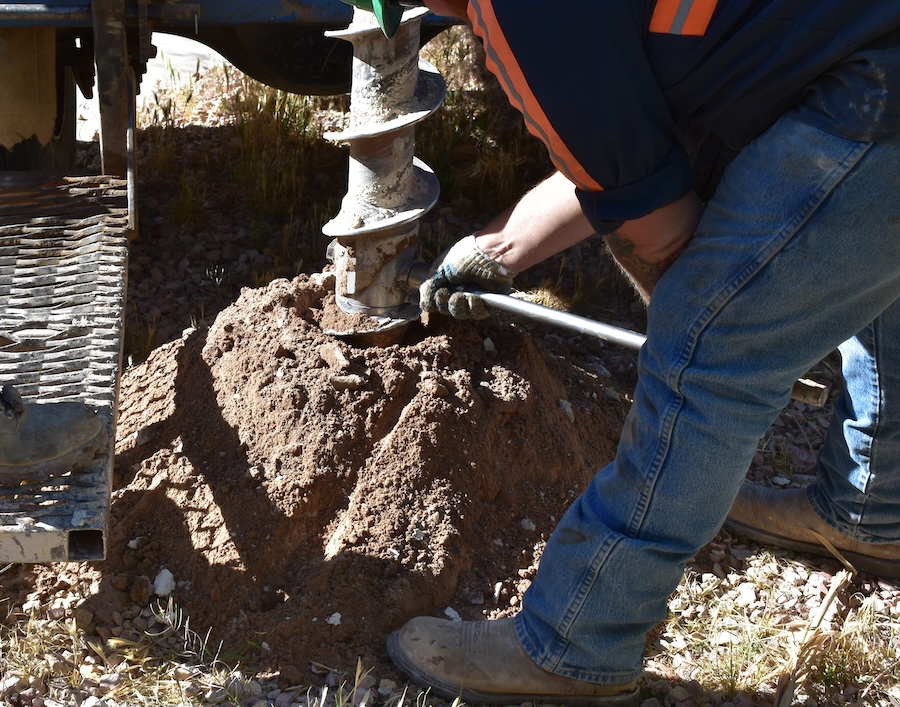
View the complete article here.
In today’s competitive and cost-sensitive foundation drilling industry, efficiency is paramount as even minor delays can lead to significant setbacks and increased expenses. This guide provides actionable tips designed to boost efficiency, reduce downtime, and optimize overall project outcomes. We outline ten key tips—ranging from thorough pre-project planning and selecting the right equipment to investing in operator training, leveraging technology, and employing effective project management strategies.
Tip #1: Optimize Auger and Attachment Selection
Selecting the right augers and attachments tailored to the specific soil conditions of your project can dramatically boost drilling performance and efficiency.
Matching Augers to Soil Types
Different soils demand different auger designs—coarse, granular soils might require a more aggressive cutting edge—while cohesive clays may benefit from smoother, slower-turning bits to avoid clogging.
Choosing the Right Attachments
In addition to augers, consider specialized attachments such as cutting heads or drilling stabilizers that can enhance performance in challenging environments. Matching these attachments to your equipment ensures optimal load transfer and drilling precision.
Equipment Integration
Ensuring that your augers and attachments are compatible with your drilling rigs and can be easily swapped or upgraded is key to maintaining versatility and responsiveness on site.
Tip #2: Customize Equipment Settings for Variable Soil Conditions
Tailoring your equipment settings to the specific characteristics of the soil can lead to more efficient drilling and reduced wear on machinery.
Adjusting Drilling Parameters
Fine-tune parameters such as rotation speed, penetration rate, and fluid injection based on soil composition to optimize cutting efficiency and minimize resistance.
Utilizing Data-Driven Adjustments
Employ sensors and real-time monitoring tools to assess soil behavior during drilling, allowing operators to adjust settings on the fly and maintain consistent performance.
Documenting Best Settings
Keep detailed records of equipment settings and performance metrics across different soil types to build a database of best practices that can inform future projects.
Tip #3: Conduct Thorough Pre-Project Planning and Site Assessment
Before beginning any drilling operation, a robust pre-project plan and comprehensive site assessment are essential for ensuring smooth execution and avoiding unforeseen setbacks.
Importance of Early Planning
Detailed planning before beginning any foundation drilling project is essential to minimize unexpected delays and enhance overall efficiency. By investing time upfront to thoroughly understand the project requirements and site conditions, you can avoid costly setbacks and ensure that the drilling process runs smoothly from start to finish.
Key Considerations
A comprehensive site assessment should cover several critical aspects—including a complete site analysis, evaluations of soil conditions, environmental factors, and potential risks. Understanding the soil composition, groundwater levels, and any environmental constraints helps in selecting the appropriate equipment and drilling techniques—while a robust risk assessment prepares the team to manage any unforeseen challenges.
Tools and Techniques
Leveraging modern tools such as geotechnical surveys and digital mapping systems can provide invaluable insights into the site’s characteristics. These technologies not only streamline the planning process but also ensure that the drilling operation is based on accurate, up-to-date data—ultimately contributing to a more efficient and successful project.
Tip #4: Choose the Right Drilling Equipment
Selecting the proper drilling equipment tailored to the project’s unique needs is crucial for maximizing efficiency and performance.
Matching Equipment to Job Requirements
Choosing equipment that aligns with the specific conditions of your project can significantly improve operational efficiency. When equipment is matched to the job requirements, taking into account factors like soil type and project scope, it minimizes downtime and ensures that the drilling process is smooth and effective.
Factors to Consider
Key considerations when selecting drilling equipment include capacity, versatility, and compatibility with the site’s conditions. Assessing these factors helps ensure that the equipment can handle the required workloads, adapt to varying conditions, and integrate seamlessly with other project components.
Expert Recommendations
Industry experts recommend looking for equipment features that enhance performance—such as advanced control systems, high-efficiency drilling bits, and robust safety mechanisms. These features not only improve drilling accuracy and speed but also contribute to long-term reliability and cost savings over the course of the project.
Tip #5: Implement Routine Maintenance and Calibration Practices
Regular maintenance and calibration of drilling equipment are essential strategies to prevent unexpected failures and ensure consistent, high-performing operations.
Importance of Maintenance
Regular maintenance is critical as it prevents equipment failures and minimizes costly downtime, ensuring that the drilling process remains uninterrupted and efficient.
Scheduling and Calibration
Establishing a systematic service schedule and calibration routine is key to maintaining optimal equipment performance—setting predefined intervals for inspections, adjustments, and part replacements can greatly enhance reliability.
Benefits
By implementing these maintenance practices, you can achieve improved reliability, reduced repair costs, and consistent drilling performance—ultimately contributing to smoother project execution and long-term equipment durability.
Tip #6: Invest in Operator Training and Skill Development
Skilled operators are the backbone of efficient and safe drilling operations, making continuous training and development a critical investment.
Role of Skilled Operators
Well-trained operators are essential for maximizing equipment efficiency and ensuring on-site safety. Their expertise not only optimizes the performance of the drilling equipment but also helps prevent accidents and costly errors.
Training Programs
Implementing effective training programs—including hands-on sessions, simulation drills, and certification courses—ensures that operators are proficient with the latest equipment and safety protocols. Structured training helps build a strong foundation of technical skills and instills a culture of safety and precision.
Continuous Learning
Encouraging ongoing education and regular skill updates is vital as new drilling techniques and technologies emerge. Continuous learning keeps operators at the forefront of industry advancements, enabling them to adapt to evolving challenges and maintain high standards of operational excellence.
Tip #7: Leverage Technology and Automation
Integrating advanced technology into drilling operations can streamline processes, improve precision, and enhance overall safety.
Modern Drilling Technologies
Incorporating digital monitoring systems, automation, and data analytics into foundation drilling operations can significantly streamline workflows. These technologies allow operators to monitor performance in real time, adjust parameters on the fly, and quickly address any issues that arise during drilling.
Benefits of Automation
Automation in drilling brings increased precision, real-time problem-solving capabilities, and enhanced safety. By reducing human error and providing immediate data feedback, automated systems help optimize drilling performance and ensure a safer working environment.
Case Examples
For instance, some drilling projects have successfully integrated remote-controlled rigs and sensor-based monitoring systems—resulting in faster decision-making and fewer operational delays. In another example, data analytics tools have been used to predict maintenance needs—thereby reducing unexpected downtime and improving overall project efficiency.
Tip #8: Optimize Drilling Parameters and Techniques
Fine-tuning the operational parameters of your drilling process can yield significant gains in efficiency and overall performance.
Fine-Tuning Operations
Adjustments in drilling speed, fluid rates, and bit selection can dramatically impact efficiency. Tailoring these factors to match the specific geological and environmental conditions of your project ensures that the drilling process is both effective and resource-efficient.
Data-Driven Decisions
Leveraging performance metrics and establishing feedback loops enables operators to make informed adjustments. Continuous monitoring and analysis of drilling data allow for real-time optimization, ensuring that parameters remain aligned with the project’s evolving needs.
Best Practices
Adhering to industry-standard benchmarks for drilling operations provides a reliable framework for success. By following established best practices—operators can achieve consistent performance improvements, reduce wear-and-tear on equipment, and maintain high levels of productivity throughout the project.
Tip #9: Employ Effective Project Management and Scheduling
Implementing robust project management and scheduling practices is essential for synchronizing team efforts and minimizing downtime throughout drilling operations.
Coordination and Communication
A coordinated approach between teams is crucial to reducing downtime. Effective communication ensures that everyone is aligned on objectives, addresses issues promptly, and optimizes resource allocation—ultimately smoothing out the entire drilling process.
Scheduling Tools
Utilizing advanced project management software and scheduling techniques tailored to drilling operations helps in planning tasks, tracking progress, and adapting to changes in real time—ensuring that timelines are met and bottlenecks are avoided.
Performance Tracking
Regularly tracking project milestones and key performance indicators (KPIs) allows teams to measure progress, identify areas for improvement, and make data-driven decisions that contribute to continuous operational enhancement.
Tip #10: Invest in Advanced Equipment Upgrades and Innovations
Staying current with the latest equipment innovations can provide a competitive edge by improving drilling performance and extending equipment lifespan.
Embracing Technological Advances
Adopt cutting-edge equipment upgrades—such as enhanced drilling rigs with improved power efficiency, better control systems, or advanced materials that resist wear and corrosion.
Enhancing Equipment Durability
Investing in modern, robust equipment reduces maintenance downtime and improves overall reliability—leading to fewer disruptions during drilling operations.
Future-Proofing Operations
Regularly review and update your equipment fleet to incorporate new technologies that offer increased precision, safety, and efficiency—ensuring your operations remain competitive in an evolving industry.
View the complete article here.
How can I improve efficiency in foundation drilling projects?
Optimize auger selection, tailor equipment settings to soil conditions, and use real-time data and planning tools to streamline operations.
Why is operator training important in foundation drilling?
Skilled operators maximize equipment performance, ensure safety, and adapt quickly to changing site conditions.