Inlet Watch Yacht Club Seawall Weeps to Relieve Pressure
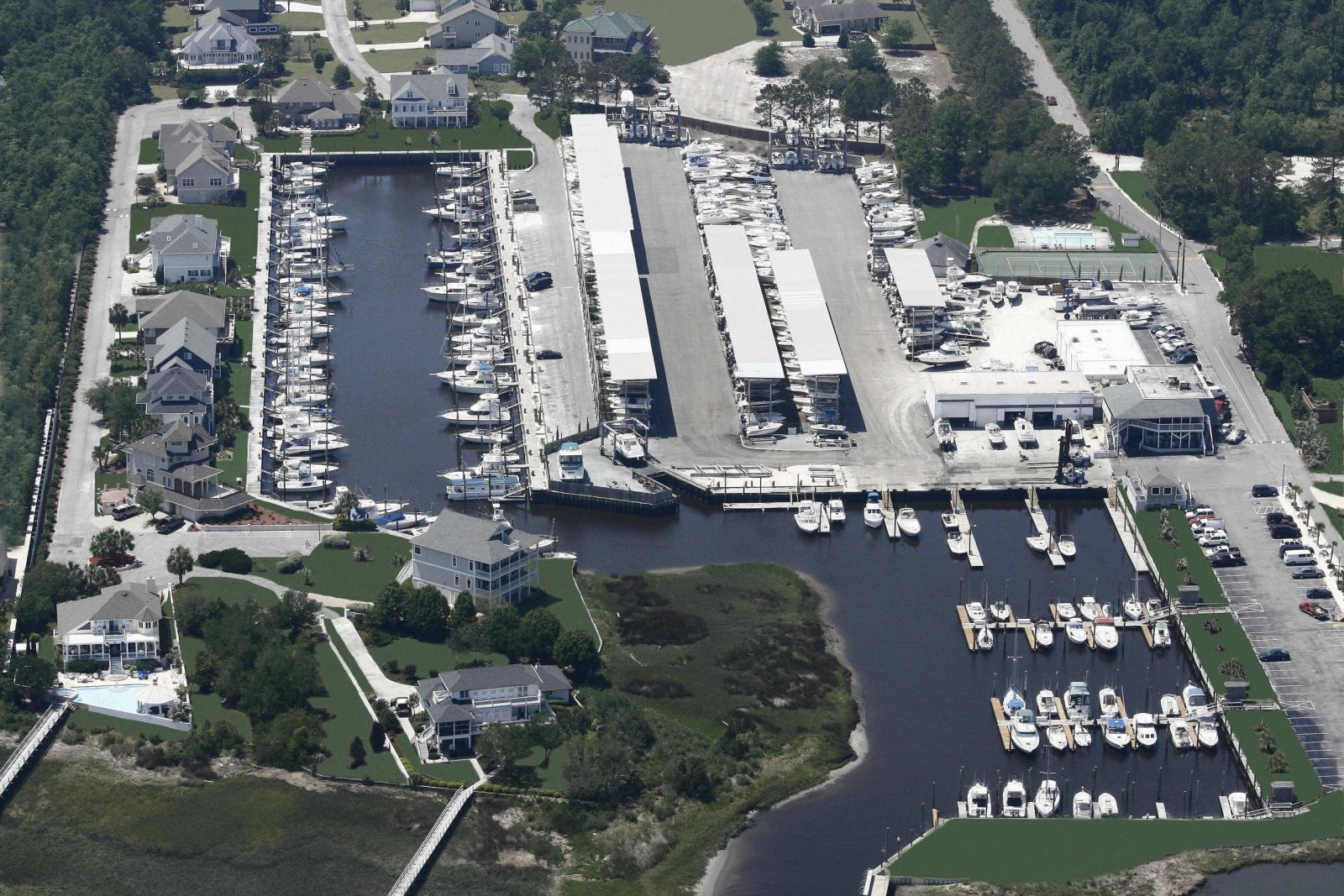
Originally published by Anna Townshend in Marina Dock Age
The seawall at Inlet Watch Yacht Club in Wilmington, N.C., is a myriad patchwork of materials of varying ages, but it lines the protected basin in the 20-acre resort as a solid structure.
Around the marina, the seawall may look different from the outside, but Troy Moore, general manager of Inlet Watch Yacht Club, worries about one specific problem behind the entire seawall facade—the water back there.
The pressure
The original facility, built in 1974, had a concrete seawall along the waterway and timber bulkheads along the inside of the basin. Hurricanes caused many acute failures that were repaired over the years. In 1996, Hurricane Fran caused more serious damage to the back basin, and the facility installed a new steel bulkhead on the south side of the basin. The storm also did damage to the north side seawall in the front basin, closest to the ocean, which was repaired with a vinyl bulkhead. In 2006, the marina continued its seawall maintenance, installing a fiberglass composite structure, opposite the steel seawall.
From doing these repairs, Moore knew the seawall had water behind it, a common problem for facilities, especially in areas with an active spring, tidal surge or rainy season. Water behind the wall isn’t inherently the problem—it would be difficult to completely block that from happening behind a waterfront structure. The problem arises when the retaining wall also retains the water behind the wall. Unfortunately, water stuck there creates hydrostatic pressure, which can cause movement in the seawall, enough to make it fail.
Additionally, the soil, sand, clay or any other material around a seawall will naturally try to erode through the wall, if it can escape with any water flow. This can create sinkholes, among the other problems associated with a seawall that has begun to separate.
As one of the more vital structures to a properly functioning marina, seawalls deserve regular attention. Most operators should observe the visible signs of problems with their seawall during normal maintenance.
For instance, on the vinyl bulkhead installed in 1997, Moore would notice a waler that was too high on the top or a bottom one that was too low. Also, bulges in the wall are sure signs that water is trapped behind the vinyl, he added.
In 2006, when Moore installed the composite bulkhead, Andrew Consulting Engineers in Wilmington, N.C., introduced him to a solution for relieving the pressure behind the wall—by installing weep hole drains called Jet Filters from Jet Filter Systems in Casey, Ill. With this design, water escapes from behind the wall through about 150 weep holes, and a filter prevents soils and sands from doing the same.
Recently, Inlet Watch Yacht Club installed 130 additional Jet Filters in its 650-foot vinyl bulkhead. That puts one weep hole about every five feet. In that area around the coast of North Carolina, especially around the root systems of live oaks, the soil often holds pockets of water. “We’d drill for one hole and find no water,” Moore said. “Others, we’d have a gusher.”
To install the Jet Filters, contractors dug a 2-foot by 2-foot section behind the wall, down about 3.5 to 4 feet deep. Moore said, the depth of the hole is dependent on the amount of freeboard at the facility, more specifically calculated to one foot above the mean water level (mid-tide). At Inlet Watch Yacht Club, with four-foot tidal shifts, it needed a deep hole. This became the most labor intensive part of the installation process.
Moore estimated it took about an hour and a half to dig behind, drill into the bulkhead, set the filter in place with four self-tapping screws, drop in approximately two square feet of 57-stone, a course aggregate, to act as an additional filter, and fill up the hole.
Despite the time spent digging, Moore still said the project was a bargain. Including the labor intensive digging and the filter, the overall project cost around $110 per weep hole.
David Gentry, owner of Jet Filter Systems, said the design of the filters could make installation even more simple because they’re designed for front installation into the seawall, without the need to dig behind the wall.
“Many facilities don’t have the ability to dig behind existing seawalls,” Gentry said. Instead, they can drill through the front, creating a small cavity behind the wall, and the filter unit goes in about four inches.
The most ideal drainage layout does involve the installation of 57-stone behind the wall, but the additional step is not necessary with the Jet Filters. Gentry said through a front installation, the filters can provide the same relief to a structure with restricted access behind the seawall.
The secret to the filter and what allows water to escape and keeps soil and sediment in is the filter material (Mirafi® from TenCate Geosynthetics). The geotextile is composed of polypropylene yarns, which are woven in such a way that they retain their relative position—in other words, the filter doesn’t wear out and it doesn’t get clogged with soils and sands.
Depending on the amount of water and the soil composition, the filter may need to be cleaned, if it’s not weeping effectively. Gentry recommends checking the holes annually. Many will never have an issue. About every three years, depending on the soil composition, some filters may need cleaning with a pressure-washer or cleaning solvent. They will always retain their integrity and filtering abilities, Gentry said. In 16 years of using this geotextile, he has never had to replace one.
Seawall for life
Inlet Watch Yacht Club, an approximately 125 wet slip and 525 dry slip facility, is part dockominium. About 580 of its slips, wet and dry, are owned, rather than rented, meaning Moore has a lot of owners to keep happy at the aging facility.
“In 2007, we did work on one of our bulkheads, replacing a timber wall, and we elected to do a price comparison between vinyl and composite,” Moore said. “They’re very similar in cost.”
He added that fiberglass composite has an added advantage in the ability to spot repair damaged parts of the wall. With vinyl sheet piling, repairs to a sheet pile require replacing the entire sheet.
Future seawall upgrades at Inlet Watch Yacht Club include new fiberglass composite and steel bulkhead. The marina’s engineering firm designed plans for steel in places that needed added strength, in this case, the areas immediately accessible to the forklift and travelift. “Apart from these areas, our engineers have confirmed that composite sheet piles would be the appropriate selection,” Moore said. The seawall upgrade plans also include Jet Filters weep drain holes to relieve the hydrostatic pressure behind the seawall and increase its lifespan.